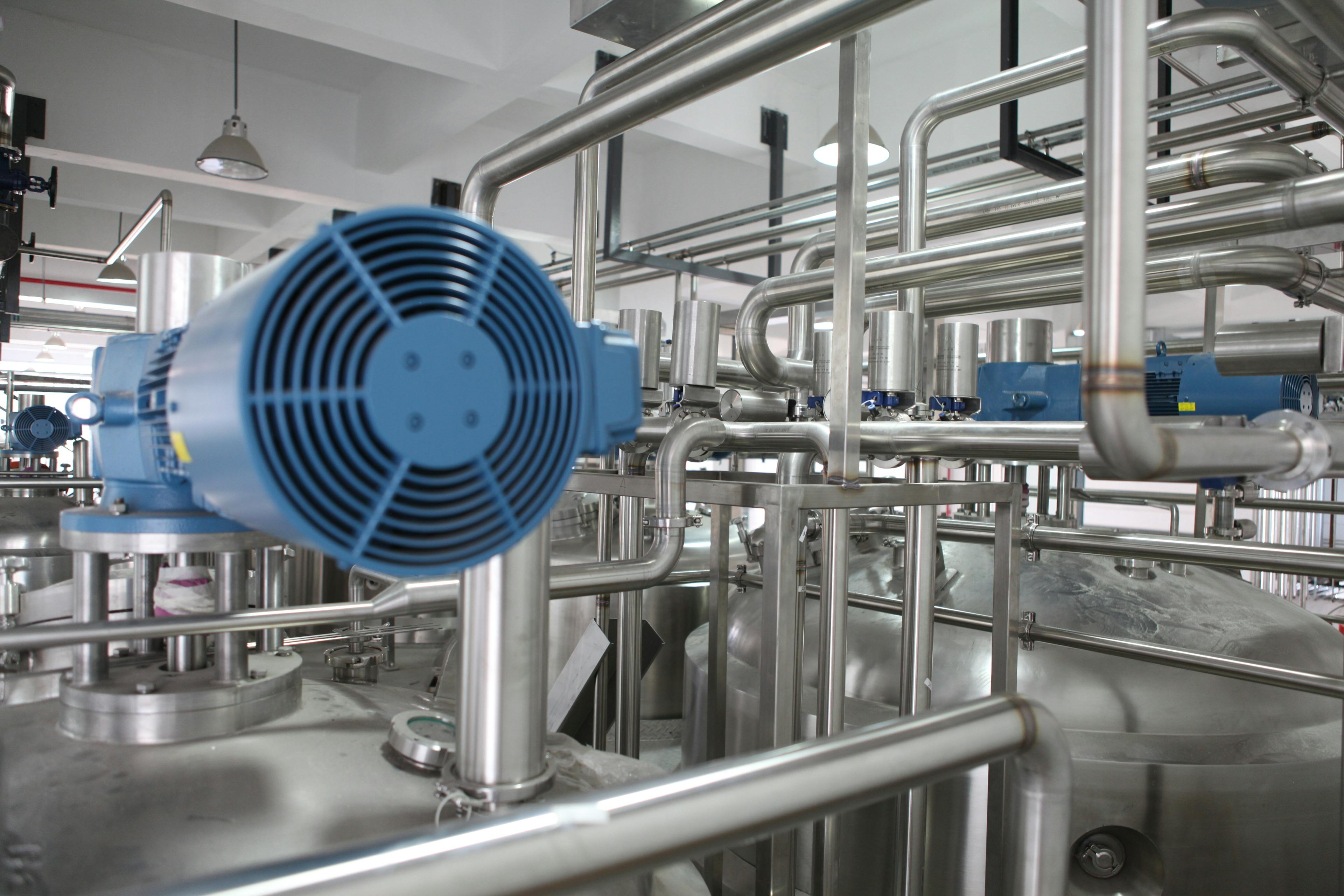
Decarbonize low-temperature industrial heat with heat pumps
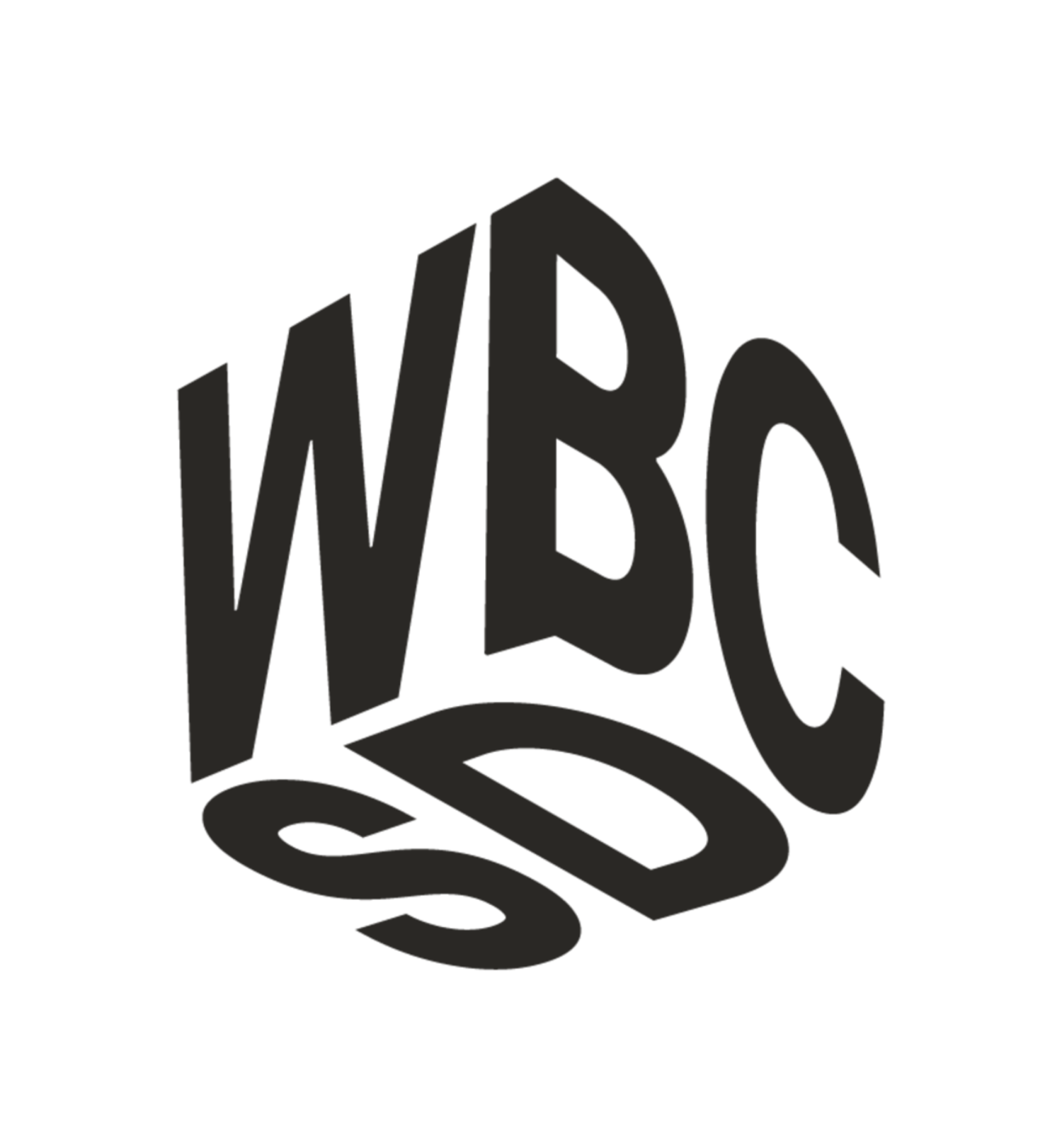
Summary
Industrial heat pumps generate low-temperature process heat with higher efficiency and lower GHG emissions than conventional fossil fuel heating options.
Key resources
Context
Process heat in industry, which refers to the energy input of thermal manufacturing processes (e.g., material transformations and chemical processes), accounts for 29% of global energy demand. Nevertheless, less than 10% of it is currently generated directly from renewable sources and 75% is still generated directly from coal, gas, and oil. Industrial heating applications vary widely in their operating temperatures, as dictated by different industrial processes, but almost half of them are served by temperatures lower than 200°C. At these temperatures, industrial heat pumps already offer high efficiency and operational cost savings. Therefore, they are emerging as the most promising heating technology for the decarbonization of these applications.
Image:Â Global industrial heat use by temperature, 2016

Source: BloombergNEF (2019). Industrial Heat Pump Primer
Solution
Heat pumps are the reverse of a refrigerator in that they transfer available heat from a colder place (heat source) to a warmer place (heat sink) by compressing a refrigerant (or working fluid) to increase the temperature to a more useful level, typically by using electrical energy. They are highly energy efficient compared to existing conventional heating options, as they deliver more thermal energy than the electrical energy put into them. The efficiency of a heat pump is described by the coefficient of performance (COP), defined as the ratio of thermal energy output to energy input. Currently, industrial heat pumps can achieve efficiency higher than 400% (i.e., COP 4). By comparison, conventional heating options always have an efficiency below 100%, meaning they always output less thermal energy compared to the energy input. Heat pumps are especially efficient when they can use waste heat from another industrial process as a heat source and upgrade it to required temperatures.
Image: : Industrial heat pump using waste heat in industry – whether from a business’ own processes or from nearby third parties

Source: WBCSD (2022)
Usage
The sector with the greatest uptake of heat pump use is the food, beverage, and tobacco sectors, where 41 heat pumps were installed across a sample of 77 global industrial heat applications in 2019. Given the sector represents more than one-quarter of all low-temperature heat demand, it will likely continue to see the greatest use of heat pumps. A more recent trend is to install heat pumps at sites that require simultaneous low-temperature heating and cooling in a combined heating and cooling solution due to higher efficiencies. Industrial heat pumps remain less common in industries that rely on both high-temperature and low-temperature processes at a given facility, such as chemicals.
Image: Sample of industrial heat pump applications by sector globally, 2019

Source: BloombergNEF (2019). Industrial Heat Pump Primer
Impact
Climate impact
Targeted emissions sources
Heat pumps can reduce Scope 1 carbon emissions by replacing fossil fuels with a renewable heat source (i.e., ambient heat from the ground, air, or a waste heat source) and using electricity sourced from an increasingly low-carbon grid to drive the pump. The heating application can be carbon free by covering the increased electricity consumption using certifiable carbon free electricity.
Business impact
Benefits
Reduced overall energy use
Heat pumps reduce overall energy use through high thermal efficiencies, especially for low-temperature heating applications and when waste heat sources can be upgraded.
Decreased operation costs
Based on forecasts by DNV(1), the electricity-to-gas price ratio will decrease in the future. Therefore, while electricity costs should remain higher than natural gas on a per-unit basis, heat pumps will yield significant reductions in operational costs, given their efficiency is two or three times that of a natural gas boiler.
Additional revenue-generating opportunities
Electrification with heat pumps can enable additional revenue-generating opportunities by providing grid-flexibility services.
Increased supply security
Heat pumps increase supply security by reducing reliance on (often) imported fossil fuels
Product quality improvements
Heat pumps can introduce product quality improvements, since a precise temperature is easier to maintain with a fully electric solution versus heat from combustible fuels.
Costs
Heat pumps often involve high capital expenditure. Moreover, companies need to integrate unfamiliar technologies into their facilities and work across internal functions to identify the most appropriate business models and financing mechanisms, which can further increase upfront costs.
However, capital costs are offset by long-term costs that are lower than conventional fossil fuel heating systems. This is driven mainly by lower operational costs, expected increases in the cost of carbon, and lowering electricity-to-gas price ratios.
Impact beyond climate and business
Co-benefits
Heat pumps enable circular solutions where one company’s waste heat can be upgraded and used by another company.
Implementation
Typical business profile
Heat pumps are most relevant for companies requiring process heat at lower temperatures (lower than 200°C), such as those in the food, beverage, and tobacco sectors, which aim to decarbonize their operations. Nevertheless, the technology is being rapidly developed with higher temperate applications already in prototype phases.
Stakeholders involved
Company functions:
Technical, financial, operations, procurement, and management expertise.
External
Heat pump provider, grid distribution system operator, electrical utility.
Key parameters to consider
Solution maturity
Heat pump technology is a mature technology and is already being applied commercially across the globe to generate temperatures up to 150°C. Heat pumps for higher temperatures are currently in the early development stages.
Technical constraints or pre-requisites:
The efficiency of a heat pump is directly related to the temperature increase required – also known as temperature lift. The greater the temperature lift between the source and the sink, the lower the coefficient of performance. Access to a waste heat source can be critical to reaching higher temperatures.
The availability of suitable refrigerants currently limits their commercial application to approximately 150°C.
Industrial heat pumps also require large amounts of electricity. Therefore, the local grid must have the capacity to deliver it.
Additional specificities
The regions with a lower electricity-to-gas price ratio and increasing cost of carbon are more favorable for heat pump deployment, due to lower operating expenditure costs compared to conventional heating alternatives using fossil fuels.
Implementation and operations tips
To ensure companies can unlock the full potential of industrial heat pumps, they should:
Seek opportunities to couple heating and cooling applications within or outside an industrial facility and leverage existing waste heat streams
Pursue opportunities to make use of variable electricity tariffs and potential revenue generation opportunities by providing grid balancing services
Embrace alternative business models and financing mechanisms such as Heat-as-a-Service
Seize opportunities to minimize disruptions and capital costs by installing heat pumps during planned outages, and at sites with no or limited additional grid connection costs
Use scenarios for utility and carbon prices to understand the lifetime costs of all options, and the policy and market risks associated with fossil fuel-based heat