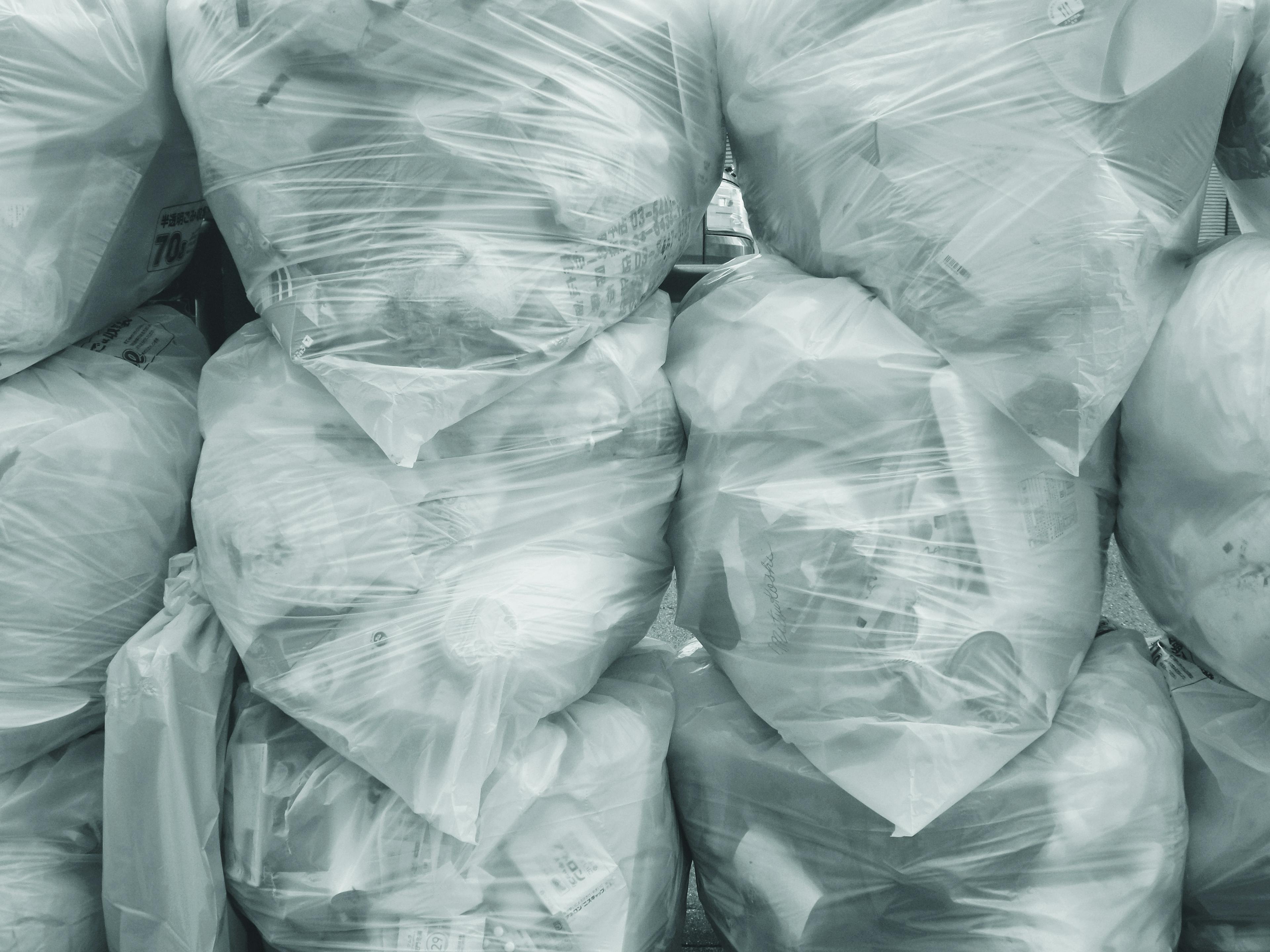
Maximize waste recovery in the pulp and paper mill
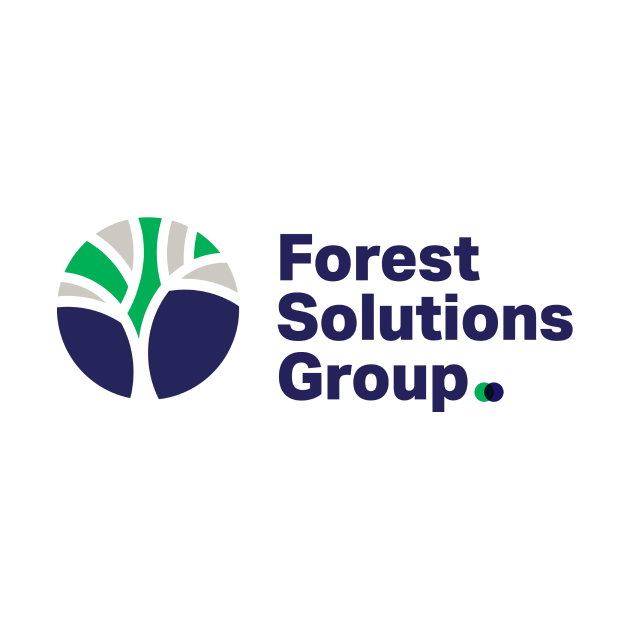
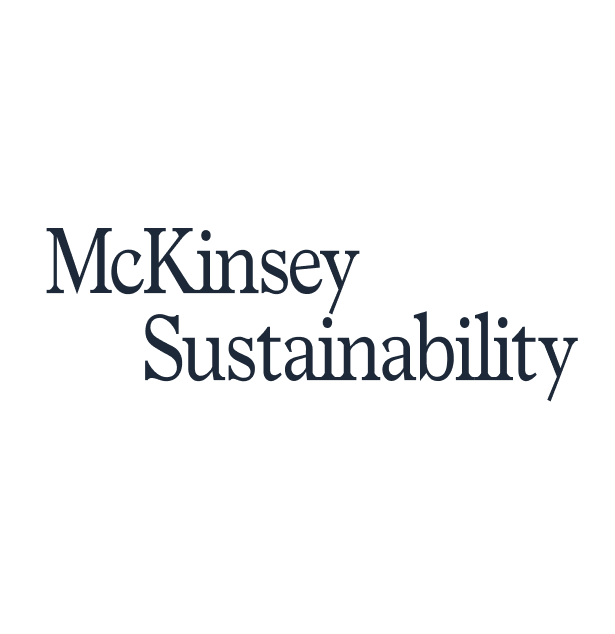
Summary
Adopting processes to recover energy from waste, such as black liquor gasification, can lead to higher resource and energy efficiency, while reducing GHG emissions
Key resources
Context
This Action is one of ten from the Catalogue of Key Decarbonization Actions, part of the Forest Sector Net-Zero Roadmap. Its objective is to support forest companies in the choice and implementation of actions to address emission hotspots and leverage the greatest opportunities for carbon removals.
LEVEL OF MATURITY | EMISSION ABATEMENT POTENTIAL | SHORT-TERM ECONOMIC FEASIBILITY | |
---|---|---|---|
LOW TO MEDIUM | LOW TO HIGH | LOW | |
• Prototype proven in test and conditions and in conditions to be deployed • TRL 4 -5 | • Depending on the configuration, BLG could reduce 3 to 100% of the lime kiln emissions | • CAPEX: 65 – 230 million EUR depending on the configuration • Abatement cost: 500 – 700 EUR/tCO2, when considering the revenues from electricity or biofuel sale |
See methodology in the appendix section
Solution
Black liquor gasification (BLG) is a process to recover energy from black liquor’s organic content, using a gasification process. In a BLG system, the recovery boiler is replaced with a gasification plant where the black liquor is converted to a synthesis gas. Black liquor is a by-product of the kraft process, in which pulpwood is converted into paper pulp by removing lignin and hemicellulose constituents to free the cellulose fibers. Black liquor has a high organic content, with an approximate energy content of 14 MJ/kg dry solids, which is about half of the energy content of 1kg of coal equivalent. Current black liquor handling uses a recovery boiler to recover the energy and chemicals from black liquor. However, even though the traditional recovery process has worked well, it also has several disadvantages, such as low efficiency (due to black liquor’s relatively high water content, which limits combustion efficiency), as well as smelt-water explosions and sulphur gas emissions.
In a BLG system, the black liquor is fed into a gasification plant, where a pressurized gasifier makes it evaporate in a high temperature and high pressure reactor. The black liquor gasification generates a so-called ’syngas‘. This is separated from the inorganic smelt and ash, which are cooled in the quench zone below the gasifier, where it dissolves to form green liquor in a manner similar to the dissolving tank of a recovery boiler. In the meantime, the hot syngas is also rapidly cooled and quenched using water or other cooling agents. The heat released as the water vapor in the syngas condenses is used to generate steam. Additionally, the condensation process removes tar and other compounds from the gas. The result is a nearly sulphur-free synthesis gas consisting of mostly carbon monoxide, hydrogen and carbon dioxide.
Moreover, different BLG technologies can be applied to recover black liquor and transform the syngas into other products:
Renewable biofuels: The synthesis gas produced from gasification can be used to produce biofuels such as DME (dimethyl ether), methanol, chemicals, hydrogen, ammonia, synthetic natural gas or synthetic diesel fuels (e.g., FT diesel). This is a good option given the growing interest in finding cheap and efficient ways to produce CO2-neutral automotive fuels.
Electricity: Generating electricity from black liquor is possible, adopting a Black Liquor Gasification Combined Cycle (BLGCC), a system that uses the synthesis gas to fire a gas turbine, in which power is generated.
Box 10: Maximizing waste recovery: other waste streams and recovery pathways
The adoption of technologies that can recover energy from waste can lead to higher resource and energy efficiency, while helping the forest sector to reduce emissions. In fact, pulp and paper mills generate energy-rich biomass as waste in many stages of the process, such as in wood preparation, in pulping and paper making, and through the wastewater treatment. The major sources of biomass in the pulp and paper mill, and the associated energy-recovery methods, include those presented below:
Waste stream | Description | Recovery method |
---|---|---|
Wood residues and other biomass | Wood residues and other biomass (e.g. bark, branches, leaves) are left from the chemical and semi-chemical pulp processes and mechanical pulp manufacture. | Recovered in biomass boilers to produce energy or in other processes. |
Primary sludge | The primary sludge is generated after removal of suspended solids during primary clarification, while the secondary sludge is the residue left after the biological treatment of the wastewater, where microorganisms are used to reduce the dissolved organic matter in wastewater. Primary sludge has comparably far more biomass, due to the presence of large proportion of woody and other organic materials. | Recovery through combustion, digestion from anaerobic bacteria or pyrolysis, to either recovery energy or recover materials for land applications (e.g. agriculture, silviculture, composting), or for material applications (e.g. cement, bio composite). |
Secondary sludge | Secondary sludge also contains residual cellulose, hemicellulose, lignin, chemical components and micro and macronutrients. However, the high water content means that it is relatively more difficult to de-water the sludge and recover energy. | |
Paper sludge / de-inking sludge | De-inking sludge is produced form the recycling of paper. It contains fibers, inorganic compounds such as ink particles (color pigments), de-inking agents, adhesive components and fillers. The heating value is low, and the high moisture of the sludge affects its ability to burn efficiently. | Paper / de-inking sludge can be recovered for energy (although very few mills incinerate paper sludge in their boilers as fuel) or for production of high grade biofuels and bio-based chemicals through biological recovery or thermal treatment (e.g. gasification). |
Usage
The pulp and paper industry does not presently use BLG technology, despite its development and operation in pilot plants in the North of Europe since the early 2000s. The technology was deployed in several plants in small, commercial, atmospheric, low temperature BLG units, meaning BLG was proven in test conditions but not deployed at larger scale (TRL 4/5). Although pilot projects have demonstrated viability, funding shortages and political disinterest led to the closure of these projects and the companies leading them (e.g., Coskata, Chemrec, Choren, Battelle, Range Fuels, TPS, and others). Despite this, the patented technologies remain potentially available.
Recently, there has been increased interest in reviving BLG within the industry due to several factors. Firstly, when thinking about replacing an old recovery boiler, implementing a BLG plant could provide higher future profits compared to installing a new recovery boiler. Secondly, the growing demand for biofuels and hydrogen could make the economics of BLG more favourable than when it was previously trialled (1) (2) (3). However, higher estimated capex compared to recovery boiler systems and reservations to spend capex on new technology may continue to limit the full scale implementation of BLG at the point of recovery boiler replacement.
A potential step forward for BLG could come from implementing a hybrid system, where a small scale auxillary BLG system is installed additionally to the recovery boiler. In fact, in the traditional kraft recovery process, the boiler recovers energy from dissolved organic material and to regenerate the cooking chemicals. Without the recovery cycle, the process would be both economically and environmentally unfeasible. However, pulp mills can often be bottlenecked by black liquor, either due to the content and impurities of the black liquor, or due to the design and capacity of the boilers. In this scenario, the existing pulp mill, delayed by its recovery boiler, but with ample capacity in other process steps, would add black-liquor processing capacity in the form of a small BLG line (~10-20% capacity of the recovery boiler). The major advantage of this set-up, besides additional pulp volumes, would be to use the flue gas from the gasification process to heat the lime kiln, reducing, or even eliminating, one of the few remaining non-biogenic sources of CO2 in modern pulp mills.
This approach would allow BLG to be phased in gradually, without forcing companies into an all or nothing decision at the end of boiler life. As BLG technology is refined trough these small-scale implementations, and as the economics of biofuels evolve, this may lead to the adoption of BLG-only black liquor systems
Impact
Climate impacts
Targeted emissions sources
Black liquor gasification could help abate emissions in different ways:
by enabling additional energy generation in the pulp mill, increasing resource and energy efficiency, reducing the fuels input into the pulping and paper making process or increasing generation of renewable biofuels and electricity for the grid
by reducing emissions from the lime kiln.
Emission abatement potential
Estimating the decarbonization impact of black liquor gasification remains challenging. Research is relatively limited and there is no scientific consensus. The abatement potential for the industry depends on whether the energy produced is consumed within the pulp mill or sold externally to the grid or market:
On site: If BLG is used to transform the syngas into biofuels, this may require additional energy, which can increase emissions. The net impact on GHG emissions on site depends on the energy sources used in the pulp mill (e.g. if predominantly biomass and clean energy were used, emission reduction will be far less). Using BLG to decarbonize the lime kiln could achieve between 3-100% of emissions reductions, depending on the mill type. Additionally, combining black liquor gasification with carbon capture and storage can lead to even greater emission reductions (4) (5).
Externally: When biofuels produced are used outside of the mill, they can substitute fossil fuels in other sectors, such as transportation, which could substantially reduce GHG emissions in these sectors. Depending on how efficiently biofuels are used by the buyers, abatement potential can be higher (e.g. hydrogen is used in the transportation sector, which has higher efficiency fuel cells).
Business impacts
Benefits
1. Revenue-generating opportunity from energy production: The introduction of BLG technology has the potential to generate an additional source of revenue for pulp mills. This is because it offers the opportunity for more efficient conversion of the liquid by-product into biofuels or biochemicals, rather than simply being burned for heat production.
By increasing on-site energy production, pulp mills can also sell energy to the power grid, positioning them as suppliers of renewable fuels in the future energy system (i). The use of BLGCC can increase energy recovery in the pulping process and double power production at the mills, with the excess electricity or other biofuels being sold to the power grid or other players (6).
Studies on BLG installation found potential revenues of EUR 70-80 million per year from the sale of either electricity or other biofuels (DME, hydrogen) from one plant (7) (8).
2. BLG can be integrated with carbon capture and storage Increased supply security: The BLG system can be integrated with carbon capture and storage technologies, which can help pulp mills achieve even greater emission reductions while benefitting from the increased revenues from selling produced biofuels or electricity.
3. Simple logistics: Another advantage of implementing black liquor gasification is the fact that no additional distribution system is required, given that the raw material for fuel production is handled within the boundaries of the pulp and paper plant.
4. Diversified energy sources: Pulp mill economics become less sensitive to pulp prices when diversified with another product (9).
Costs
1. Investment required: BLG is two to three times as expensive in capital costs relative to a conventional recovery boiler. The capital costs for BLG were estimated to range between 65-230 million EUR depending on the different end use configurations: the lower bound is for a hybrid configuration, where the BLG plant is complementing the recovery boiler (10).
2. Operating costs: Theoretical studies suggest operating costs for the hybrid BLG system could be around 60 million EUR/year, where about half of the costs are for heat production for the gasifier, and about a third are for the purchase of the black liquor itself. In fact, the configuration in this theoretical study is so that the mill must purchase additional black liquor, either for the gasification or, in a hybrid configuration, to be burnt in a recovery boiler to supply steam to the various processes in the mill.
3. Indicative abatement cost: There are only studies on abatement costs for the hybrid configuration of the BLG system, and only considering the abatement potential within the boundaries of the pulp mill. If potential revenues from selling electricity or biofuels are factored into the calculations, the indicative abatement cost ranges between 500-700 EUR/tCO2e. Opportunities exist to couple gasification with carbon capture, thus reducing costs.
However, excluding revenues from the equation would result in significantly higher abatement costs, ranging between 5,000-8,000 EUR/tCO2e. This is due to the fact that the abatement potential of the BLG system is limited in absolute terms (excluding biogenic emissions, it can reduce emissions from the lime kiln by 4,000-10,000 EUR/tCO2e depending on the configuration) relative to very high operating costs (~yearly 60 million EUR).
The BLG system's limited abatement potential in absolute terms and high operating costs offers low short-term economic feasibility as a solution for decarbonizing the pulp mill only. However, this does not imply that it is an ineffective solution overall. The system's ability to generate green electricity and renewable biofuels has the potential to yield substantial revenue for the mill and contribute to decarbonization beyond the mill's scope, providing a lever for mitigating fossil fuel emissions and climate change.
Potential co-benefits and side effects
Co-benefits
Reduce delays in the black liquor recovery process: In the hybrid system, black liquor gasification could reduce the excess amount of black liquor that needs to be handled, thereby enabling higher productivity on top of reducing GHG emissions.
Side effects
Additional investments in steam system: Additional steam system requirements for pulp (or paper) drying may be needed due to the BLG’s lower output of high temperature steam, however this could be overcome by additional biomass steam generation, lower steam demand through steam system efficiency increase and/or implementation of heat electrification e.g. heat pumps powered by green electricity.
Additional lime demand: The calcium (lime) balance of the whole pulp mill system must be carefully studied as research suggests a lower recover of chemicals from green liquor when using BLG. Additionally, the gasification process results in more sodium in the green liquor and increased demand for lime. Estimates suggest a 16-25% additional lime demand in BLG compared to recovery boilers (11). However, in a hybrid system, where 80-90% of black liquor is still processed by the recovery boiler, this loss would drop to only 1.6-5% of total increased lime demand.
Implementation
These are the most common steps to implementing black liquor gasification in the pulp mill:
Identify and select suitable technology: Identify and select a suitable black liquor gasification technology that aligns with the mill's requirements. There are several gasification technologies available, such as entrained flow gasification, fluidized bed gasification, or indirect gasification. Suitable technology can be selected based on factors such as feedstock characteristics, desired gas composition, system efficiency, and environmental performance. Given the unique circumstances of each pulp and paper mill, companies may benefit from engagement with engineering experts.
Adapt existing infrastructure: Determine and carry out any modifications or additions necessary for implementing black liquor gasification. Gasifiers, gas cleaning systems, syngas utilization equipment, and other ancillary systems may need to be installed or upgraded.
Install and commission the plant: Execute the construction phase based on the technology's design. Coordinate with contractors and vendors to ensure correct installation of equipment and systems. Following construction, conduct thorough testing and commissioning to verify the functionality and performance of the black liquor gasification plant.
Key challenges/hurdles
Low maturity of technology: Black liquor gasification technologies are still in the initial stages of maturity (TRL of 4-5), which complicates their implementation.
Issues with quality of black liquor: The availability and quality of black liquor, the primary feedstock for gasification, can pose challenges. Also, the composition of black liquor can vary depending on the pulping process and wood sources, which may impact gasification performance.
Potential solutions
Invest in R&D: Continued research and development efforts are crucial for improving black liquor gasification processes. These efforts should focus on developing innovative gasification technologies, advanced materials, and more efficient and cost effective gas cleaning and conditioning techniques. Collaborative research partnerships between industry, academia and government institutions can drive innovation in this field.
Engage with academia to identify appropriate black liquor sources: Industry engagement with researchers to test how different compositions of black liquor affect gasification performance can help establish high quality black liquor sources and develop a plan for their supply.
Footnotes
(i) Note: IEA (2007). Black Liquor Gasification. Summary and Conclusions from the IEA Bioenergy ExCo54 Workshop
Going further
Check out other Actions as part of the Forest Sector Net-Zero Roadmap:
Appendix
Methodology for assessment against criteria
Level of maturity: The level of maturity score for each action is based on the ‘Technology Readiness Level’ (TRL). This indicator estimates the maturity of technologies, measured through an assessment of their progress and capabilities. The scale originally ranges from 1 to 9, where TRL 1 is the lowest and TRL 9 is the highest. When a technology is at TRL 1, scientific research is underway and results are being translated into future research and development, while at TRL 9 the technology has already been proven to work. The International Energy Agency (IEA) has extended the TRL scale used in this report to incorporate two additional levels of readiness: one where the technology is commercial and competitive but needs further innovation efforts for the technology to be integrated into energy systems and value chains when deployed at scale (TRL 10). Finally, there is a level where the technology has achieved predictable growth (TRL 11).
Emission abatement potential: The emission abatement potential of each action, whether a technology or practice, describes the potential to reduce GHG emissions with respect to the counterfactual technology or practice, meaning the technology or practice that is part of the ‘business as usual’ scenario, or that is substituted or improved by adopting a decarbonization action. Emission abatement potential is usually expressed as a percentage, and the higher it is, the higher GHG emission reductions can be achieved:
Low = < 15% of GHG emissions Medium = 15-50% of GHG emissions High = > 50% of GHG emissions
Abatement cost: The abatement cost is an indicator that measures the costs associated with abating one ton of GHG emissions (EUR/ton CO2e abated). The lower the abatement cost, the cheaper it is to reduce emissions, and therefore the more attractive the action.
Short-term economic feasibility: Economic feasibility is assessed based on the maturity level and the abatement cost of each action, as per the visualization below. Actions with a low maturity level (≤ 4) are considered to have low economic feasibility in the short term, given the need to validate and deploy the technology in relevant environments. However, if the abatement cost has already proven to be low, the action is assessed as medium. Actions with medium maturity (TRL 5-8) may have low or medium economic feasibility in the short term, depending on the abatement cost (≤ 250 EUR/tCO2e). Similarly, the short-term economic feasibility of actions with higher maturity (TRL 9-11) varies depending on the abatement cost (low when < 550 EUR/tCO2e, medium if the cost ranges between 250-450 EUR/tCO2e, or high if the cost is lower than 250 EUR/tCO2e). The thresholds that determine short-term economic feasibility are defined by taking into consideration that additional benefit, including revenue generating opportunities. They are not monetized or included in the abatement cost estimates.