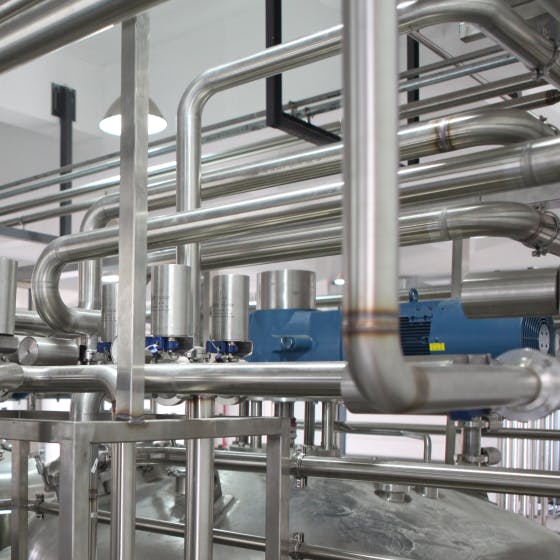
Reduce furnace CO2 emissions with a heat exchanger
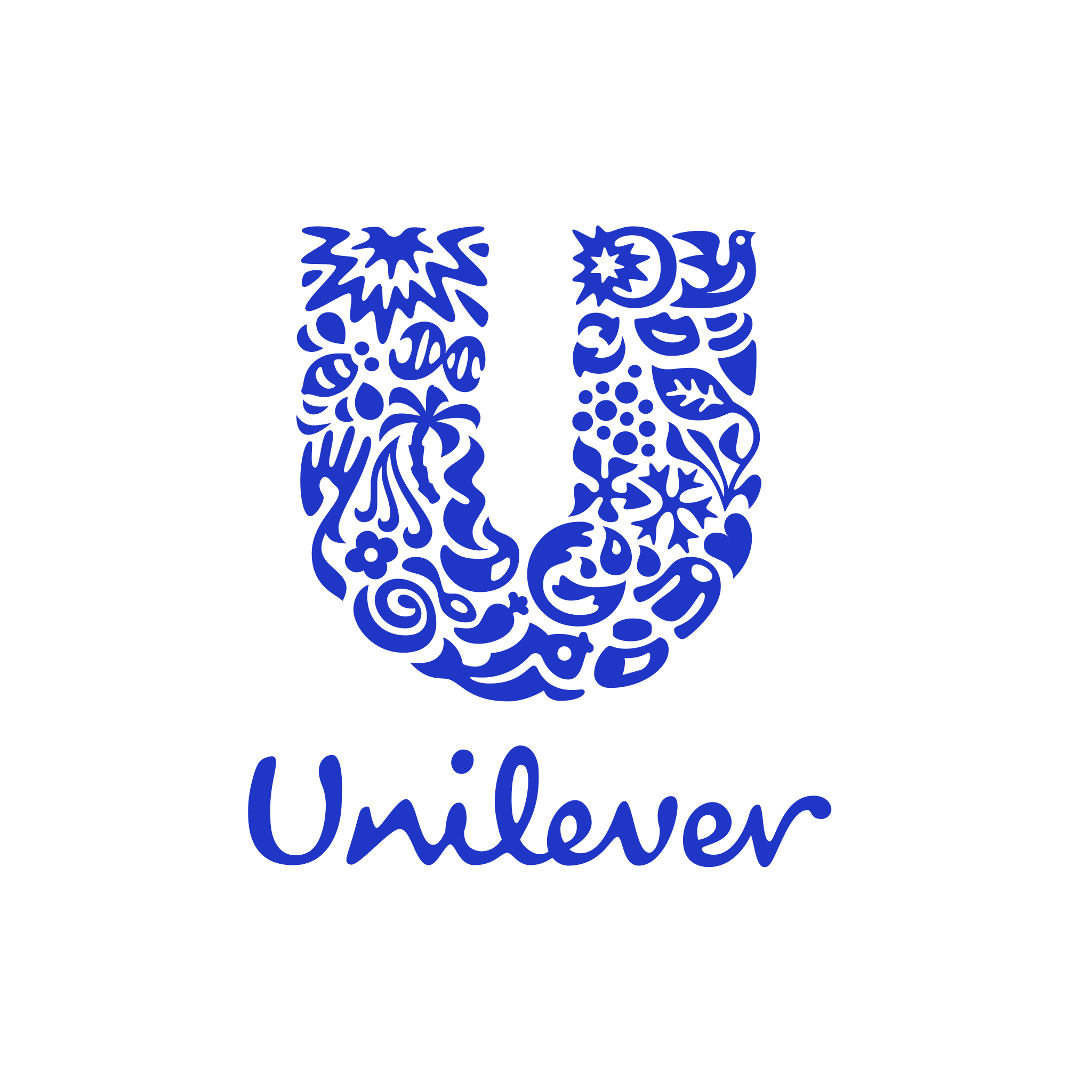
Summary
Installing a Heat Recovery Tower recovers generated heat and reduces HFO (heavy fuel oil) consumption, reducing costs and with no impact on production
Context
Unilever’s Unisola Plant, located in El Salvador, is the detergent powder sourcing unit for all its Central America & Caribbean markets. One of the main pieces of equipment in the detergent process is the Spray Drying Tower, in which hot air is generated by means of a heavy fuel oil (HFO) fueled furnace. Some 29.7% of the heat was previously lost in exhaust gases, after slurry moisture content (27 – 30%) was reduced to 3%. This final temperature of the exhaust gases was 82°C. The company therefore sought a more efficient solution to reduce waste and HFO consumption.
Additionally, Unilever plans to replace costly HFO with biodiesel to transition to 100% renewable heat at the factory (local HFO costs are dependent on international crude oil prices).
Solution
In 2020, by installing a plate-to-plate heat exchanger, Unilever was able to recover the waste heat and return it to the Spray Drying Tower, ensuring it does not go to waste. This also reduces the amount of HFO consumed. The company used two turbines for clean air and two heat exchangers. With civil reinforcement, the total weight for the heat exchangers was 5 tonnes.
Image 1: Heat recovery tower

Impact
Climate impact
Targeted emissions sources
Scope 1 emissions
Decarbonization impact
GHG emissions and energy reduction due to reduced use of HFO
Impact on GHG emissions: -550 tonnes CO2/year
Annual energy saving: -9,000 GJ/year
Business impact
Benefits
Annual financial savings: €125,000/year
No impact on production
Costs
Investment required: €385,000
Implementation
Stakeholders involved
Solution provider: Heat exchanger supplier, Gupex
Company functions: Manufacturing, Procurement, Engineering, Global Sustainability Team
Key parameters to consider
Technical considerations
Heat exchanger type
Building structural analysis for additional weight
Chemical and physical characterization of exhaust gases
CIP (clean in place) for heat exchangers, water reuse in the detergent process
Internal pressure of the heat exchanger
Dew point at the heat exchanger exhaust
Main challenges
Dust accumulation inside the heat exchanger and the cleaning process
Lightest possible heat exchanger was needed and suitable chemical properties of the construction material to prevent early deterioration