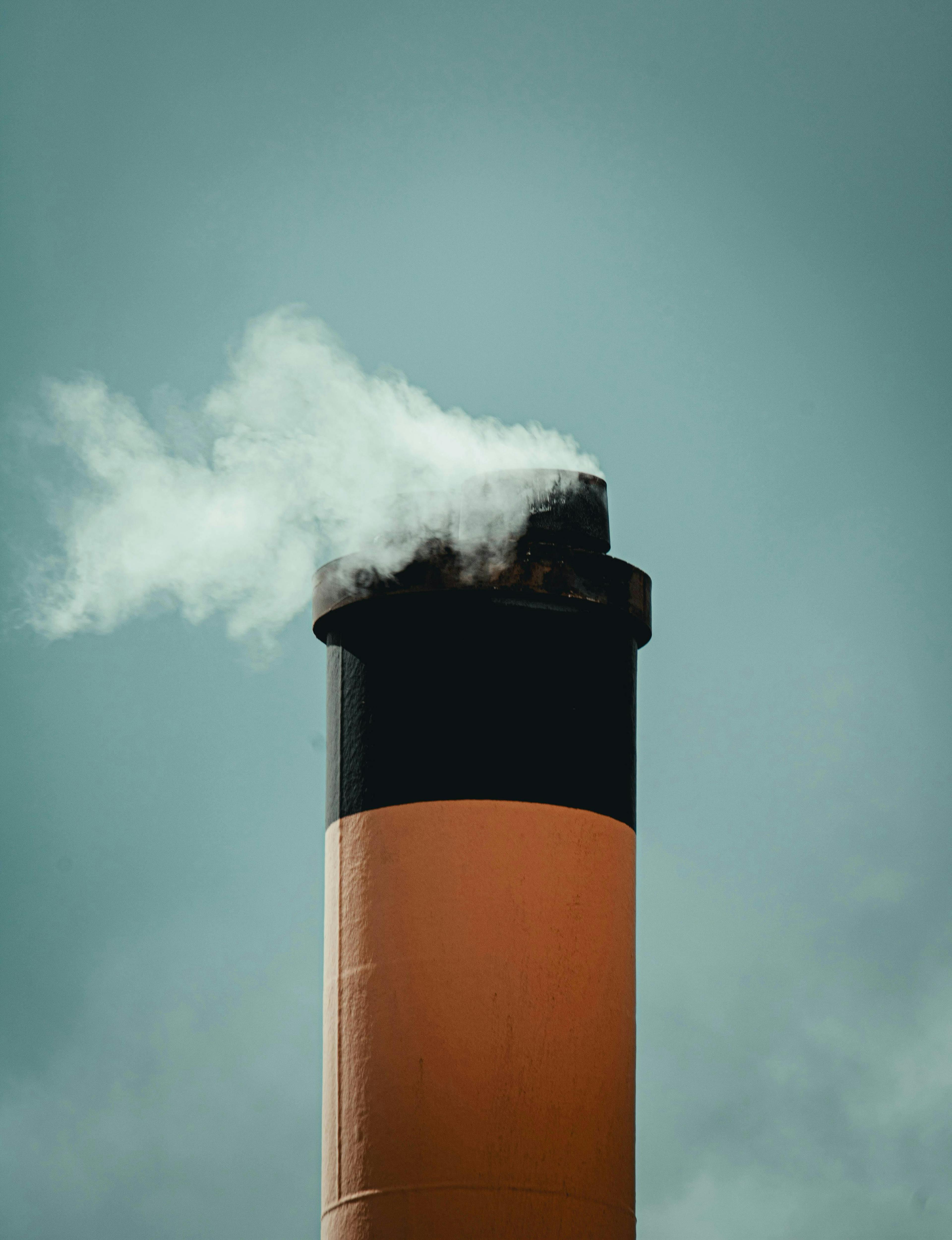
Switch to low-carbon fuels: deep dive on low-carbon hydrogen
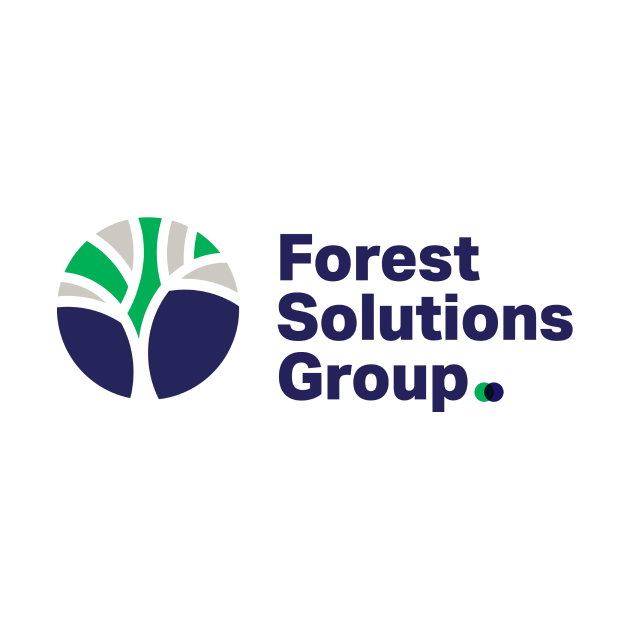
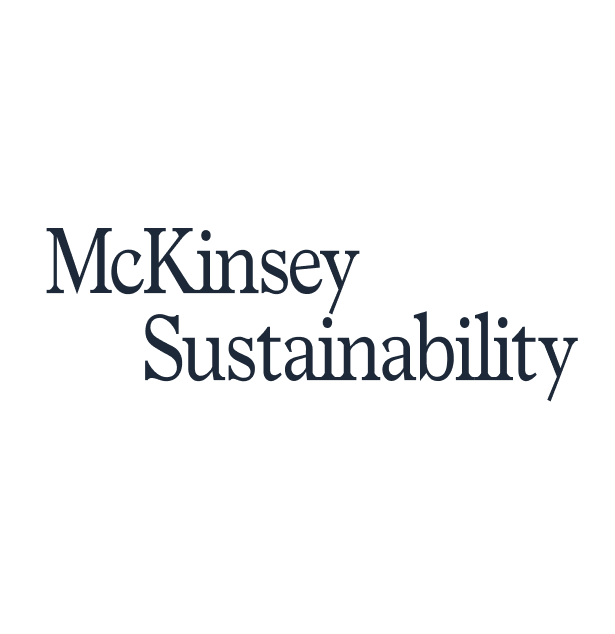
Summary
Low-carbon hydrogen has several advantages as a fuel, as it does not emit CO2 into the atmosphere when burned and can be stored in large volumes compared to electricity
Key resources
Context
This Action is one of ten from the Catalogue of Key Decarbonization Actions, part of the Forest Sector Net-Zero Roadmap. Its objective is to support forest companies in the choice and implementation of actions to address emission hotspots and leverage the greatest opportunities for carbon removals.
LEVEL OF MATURITY | EMISSION ABATEMENT POTENTIAL | SHORT-TERM ECONOMIC FEASIBILITY | |
MEDIUM | HIGH | LOW | |
• Large prototype to first of a kind commercial • TRL: 5-8 | • 100% operation emissions reduction compared to fossil fuel-powered boilers | • CAPEX: 100 – 250 EUR/kW • Abatement cost: 400 – 1300 EUR/tCO2 |
See methodology in the appendix section
Solution
As a fuel, hydrogen has several advantages. It is an abundant chemical element in nature (although typically only available in molecular forms such as water and organic compounds, and therefore not immediately available), and does not emit CO2 into the atmosphere when burned. It can also be stored in large volumes in comparison to electricity. Hydrogen is appealing for the pulp and paper industry, as it can be derived from the generation of bleaching chemicals or as a by-product from the pulping process as the mill sludge can be used to produce hydrogen through anaerobic digestion. Importantly, this produces a gas mixture consisting mainly of methane, which needs to be upgraded to biomethane, before the hydrogen can be separated out.
Hydrogen-fuelled boilers use hydrogen instead of other higher-emission fuels to generate temperatures between 300-500°C for producing steam in pulp and paper mills (1). They can be used in other phases of the forest products value chains, such as in textile manufacturing. However, adoption in the pulp and paper manufacturing segment offers the most synergies and benefits.
The switch to hydrogen as fuel for combustion boilers can occur in two ways:
by converting/retrofitting traditional fuel-powered (e.g. natural gas) boilers to accommodate hydrogen gas properties, making the boilers ‘hydrogen-ready’ or ‘hydrogen-only’ (see Box 7), or
by replacing conventional (coal, gas) fuel-powered boilers with new ‘hydrogen-ready’ or ‘hydrogen-only’ boilers.
In the case of conversion of industrial boiler into hydrogen ready boilers, several parts of the boiler must be converted to accommodate the properties of hydrogen, such as the flame detector, the pipework, and the burner.
Box 1: Hydrogen for low, medium or high heat?
In global net zero scenarios, hydrogen is expected to play a vital role in achieving carbon neutrality, and industry is expected to be one of its largest consumers. However, the specific industrial uses for hydrogen vary, and its use is more or less recommended depending on the industry.
The application and demand of hydrogen across industries varies due to several considerations, including the existence of alternatives such as direct electrification. In fact, electric heating, and particularly heat pumps, offer superior energy performance compared to any gas technology, as well as compared to hydrogen. Despite the common perception that electric technologies may face limitations in reaching the high temperatures needed for medium- and high-heat industries, some electricity-based technologies can in fact achieve high-temperatures (for instance, an Electric Arc Furnace for steel production can achieve temperatures above 1500 °C). And in fact, in the case of pulp and paper mills, which utilize medium-temperature heat (temperatures up to 400 °C), electric boilers and heat pumps are likely to offer greater efficiency and to be more economically viable. Hydrogen may in fact have a more significant role to play in industries where hydrogen is needed as feedstock or a reagent (e.g, production of steel and chemicals, including plastics and fertilizer), where hydrogen is either a reagent or a feedstock.
However, hydrogen remains an interesting lever for industrial heat decarbonization, especially given that hydrogen may be more scalable than any other technology given its many applications across sectors (e.g., power, industry, transportation, buildings). This, together with the possibility for pulp mills to produce hydrogen on-site as a by-product, could make hydrogen an applicable lever.
Box 2: Other fuel-switching actions
Low-carbon hydrogen is part of a suite of fuel-switching technologies being considered to lower emission from fossil fuel combustion in boilers in pulp and paper mills by switching to lower emission fuels, such as:
Biomass - Although the pulp and paper industry already largely uses forest biomass, pulp mills can increase and optimize the use of biomass from woody residues, such as sawdust, barks, pins and fines from chip screening, and other wood residues, in order to increase the share of renewable energy sources.
Other biofuels - In addition to woody biomass,other biofuels can be used, such as clean methane (also known as biomethane), biogas or black liquor. The advantage for pulp and paper mills is that biogas and biomethane can be produced within the pulp and paper mill directly from by-products.
Natural gas - While burning natural gas does emit greenhouse gases, it contains far less CO2 and air pollutants than many of the fuels it is increasingly replacing, especially coal. Switching from oil or coal to natural gas would therefore lead to lower emissions,
although the reduction in emissions is unlikely to be large enough for companies to reach
relevant decarbonization targets. Hence, switching to renewable energy sources should be preferred over natural gas, even in the short term, if companies are to meet their decarbonization targets.
Box 3: Definitions
To ensure all hydrogen produced and used has the lowest possible carbon intensity and is consistent with the 1.5°C scenario and net-zero scenario in 2050, WBCSD recommends the following taxonomy (on a full life-cycle basis), adding where relevant the source of primary energy (for example renewable):
Reduced-carbon hydrogen ≤ 6 Kg Co2eq/Kg H2 only relevant as a stepping stone to achieving lower carbon hydrogen for existing higher intensity production installations
Low-carbon hydrogen ≤ 3 Kg Co2eq/Kg H2
Ultra low-carbon hydrogen ≤ 1 Kg Co2eq/Kg H2
Greenhydrogen is obtained from water electrolysis using electricity produced with renewable sources. Hydrogen can be procured from external sources or produced onsite. In case of hydrogen electrolysis, any production surplus can also be sold to other industries/grid. If only green hydrogen is used, the emissions from the boilers would approach zero, but not reach it due to the remaining embodied emissions released during the lifecycle of the boilers. Green hydrogen can qualify as ‘low, or ultra low-carbon hydrogen’ when the carbon intensity meets the above threshold.
Hydrogen-ready boilers can be defined as equipment that is optimally designed to run on 100% hydrogen but initially configured to run on natural gas. This equipment may require a minimum number of components to be changed at the point of switchover but will have been specifically developed to facilitate this process (2).
Hydrogen-only boilers: Hydrogen-only boilers are entirely fuelled by hydrogen.
Usage
The adoption of hydrogen-ready and hydrogen-only boilers in the pulp and paper industry is currently low, as the maturity of hydrogen-ready boilers is also medium (TRL 5-8).
Hydrogen-ready boilers are under development, mostly designed to accommodate an initial 20% blend of hydrogen (complementary to natural gas). Industrial hydrogen-fuelled boilers are expected to be ready for a wider market by 2025, and ready for the mass market by 2035. Hydrogen-only boilers are not yet commercially available, although pilot projects exist (3).
The technology costs, the lack of uptake, high electricity prices (sometimes reaching 70% of total costs) and lack of renewable hydrogen certification are all major limiting factors. This may change as there are currently over a hundred hydrogen project initiatives in industry, transportation, built environment and energy sector, which are expected to accelerate technology development. The realization of all the projects in the pipeline could lead to more than 24Â million tonnes of low emission hydrogen produced annually by 2030, 40% higher than the expectation from 2022 (i)(4).
Impact
Climate impacts
Targeted emissions sources
Switching to hydrogen-fuelled boilers abates emissions from combustion of fuels for heating.
Emission abatement potential
Switching to hydrogen-fuelled boilers would abate 100% of the operational emissions compared to fossil fuel-powered boilers. However, some emissions are associated with boiler production, the production and transport of hydrogen. Nonetheless, this remains a low carbon emissions option.
Business impacts
Benefits
Reduced carbon costs: Reduced carbon costs in countries where a carbon price is applied to industrial emissions, in the form of a carbon tax or an emissions trading scheme. Small facilities may already be exempt.
Revenue-generating opportunity of producing and selling hydrogen: Hydrogen produced in pulp mills can be used on-site or sold to other end users if hydrogen pipes are available or road transport is a viable option.
Increased supply security: Supply security is increased by reducing the reliance on (often) imported fuels.
Costs
Investment required: The upfront investment for a new hydrogen-ready boiler ranges between 100-250 EUR/kW for capacities between 50-300 MW. The cost of converting existing boilers to hydrogen ready ranges between 6-20 EUR per kW, with prices expected to decrease marginally in the next decades. The conversion may cost approximately 20,000 EUR for a 1MW capacity boiler to almost 50,000 EUR for 10MW boiler and 160,000 EUR for a 25MW boiler. At higher capacities, boiler equipment tends to become bespoke due to additionalities requested by end-users, therefore higher costs are expected for upfront equipment leading to a higher premium at these capacities. Depending on the capacity of the boiler it may be more cost-effective to install a hydrogen-ready industrial boiler than to install a natural gas industrial boiler and subsequently convert it to hydrogen-ready (5).
Operating costs: Costs for hydrogen fired boilers include maintenance, spare parts, labour, and overheads. Fixed operating costs were estimated to be 15-20% higher for hydrogen fired boilers compared to natural gas. This is due to the increased cost in technical and safety requirements involved in the use of hydrogen (6). Variable costs depend on energy prices. Costs for renewable hydrogen are expected to decrease as production scales up, while costs for end users could drop by 50% from 2020 to 2030 (see Figure 1), which will also likely lower prices (7).
Indicative abatement cost: The abatement cost of hydrogen-fuelled boilers is largely dependent on the prices of hydrogen. High-level estimates are at 400-1,300 EUR/t CO2e (ii).
Figure 1: Projected global production costs of hydrogen, USD / kg (8)

Potential co-benefits and side effects
Co-benefits
Storage: One of the advantages of hydrogen, is that it can be stored (similarly to electricity in e.g. Thermal Energy Storage). While the costs for hydrogen storage are currently high for it to be economic, once this option becomes economically attractive, hydrogen can be distributed continuously in pipelines to support a reliable supply of renewable energy.
Side effects
Energy efficiency losses: Renewable hydrogen is produced by water electrolysis using electricity produced from renewables. Electrolyser systems today can achieve 70% efficiency, meaning that there is an energy loss for every unit of hydrogen produced from electricity (9). Technology is advancing and further improvements in the electrolysis electrical efficiency could be achieved. However, this is currently a challenge for production, making hydrogen a non-competitive option.
Safety risk: Hydrogen is a small, light gas that requires special equipment and procedures due to its ability to diffuse into certain materials, increase the chance of pipe failure, and escape easily through sealings and connectors. Its high flammability, broad ignition range, and low ignition energy make it challenging to handle safely, and detecting leaks is difficult due to its lack of colour and odour. Compared to other energy carriers, protocols for safe handling and refuelling infrastructure for hydrogen remain complex and unfamiliar, requiring more standards and regulation if it were to be used widely in the energy system.
Implementation
These are the most common steps to switch to green hydrogen:Â Â
Identify hydrogen sourcing strategy: Identify whether on-site generation via electrolysis or offsite procurement is the most feasible sourcing strategy. This selection may depend on local infrastructure e.g., neighbouring industrial clusters investing in hydrogen hubs, in addition to cost.Â
Adapt existing infrastructure or install new technology: Upgrade the existing boiler systems to ensure safe and efficient hydrogen utilization, or replace conventional fuel-powered boilers with new ‘hydrogen-ready’ or ‘hydrogen only boilers’.Â
Commission boilers: Perform initial start-up procedures, testing the boilers for proper operation and verifying their performance according to the design specifications. Complete necessary adjustments to optimize use.Â
Key challenges/hurdles
High costs: Besides energy prices, the setting up of transport and storage infrastructure is associated with significant cost (10)
Lack of expertise: Not all organizations are equipped with the experts necessary to tap into the full potential of hydrogen. This is especially an issue given low maturity levels and the need to create new hydrogen transport and storage infrastructure.  Â
Need for renewable capacity: the deployment of hydrogen for the decarbonization of industry and transport will require the deployment of renewable capacity at scale. IRENA predicts that in a net-zero scenario, in 2050 about 23% of the 90,000 TWh/year of global electricity production would be dedicated to hydrogen production.
Potential solutions
Partner with industrial clusters: Partnering with industrial clusters for the development of a hydrogen hub may help reduce distribution costs.Â
 Develop internal expertise: To ensure effective application of hydrogen in the production process, companies can recruit experts in hydrogen application either directly or hire experts to train the existing workforce.Â
Advocate for supportive policy: Organizations can engage with relevant industry bodies to raise government awareness about the environmental benefits of hydrogen in view of supporting the establishment of regulation and economic policy to incentivize deployment.
Footnotes
(i) Note: Rademaker K., Marsidi M. (2019). Decarbonisation options for the Dutch paper and board industry. PBL Netherlands Environmental Assessment Agency & ECN part of TNO, The Hague
(ii) Note: McKinsey analysis
Going further
Check out other Actions as part of the Forest Sector Net-Zero Roadmap:
Appendix
Methodology for assessment against criteria
Level of maturity: The level of maturity score for each action is based on the ‘Technology Readiness Level’ (TRL). This indicator estimates the maturity of technologies, measured through an assessment of their progress and capabilities. The scale originally ranges from 1 to 9, where TRL 1 is the lowest and TRL 9 is the highest. When a technology is at TRL 1, scientific research is underway and results are being translated into future research and development, while at TRL 9 the technology has already been proven to work. The International Energy Agency (IEA) has extended the TRL scale used in this report to incorporate two additional levels of readiness: one where the technology is commercial and competitive but needs further innovation efforts for the technology to be integrated into energy systems and value chains when deployed at scale (TRL 10). Finally, there is a level where the technology has achieved predictable growth (TRL 11).
Emission abatement potential: The emission abatement potential of each action, whether a technology or practice, describes the potential to reduce GHG emissions with respect to the counterfactual technology or practice, meaning the technology or practice that is part of the ‘business as usual’ scenario, or that is substituted or improved by adopting a decarbonization action. Emission abatement potential is usually expressed as a percentage, and the higher it is, the higher GHG emission reductions can be achieved:
Low = < 15% of GHG emissions Medium = 15-50% of GHG emissions High = > 50% of GHG emissions
Abatement cost: The abatement cost is an indicator that measures the costs associated with abating one ton of GHG emissions (EUR/ton CO2e abated). The lower the abatement cost, the cheaper it is to reduce emissions, and therefore the more attractive the action.
Short-term economic feasibility: Economic feasibility is assessed based on the maturity level and the abatement cost of each action, as per the visualization below. Actions with a low maturity level (≤ 4) are considered to have low economic feasibility in the short term, given the need to validate and deploy the technology in relevant environments. However, if the abatement cost has already proven to be low, the action is assessed as medium. Actions with medium maturity (TRL 5-8) may have low or medium economic feasibility in the short term, depending on the abatement cost (≤ 250 EUR/tCO2e). Similarly, the short-term economic feasibility of actions with higher maturity (TRL 9-11) varies depending on the abatement cost (low when < 550 EUR/tCO2e, medium if the cost ranges between 250-450 EUR/tCO2e, or high if the cost is lower than 250 EUR/tCO2e). The thresholds that determine short-term economic feasibility are defined by taking into consideration that additional benefit, including revenue generating opportunities. They are not monetized or included in the abatement cost estimates.