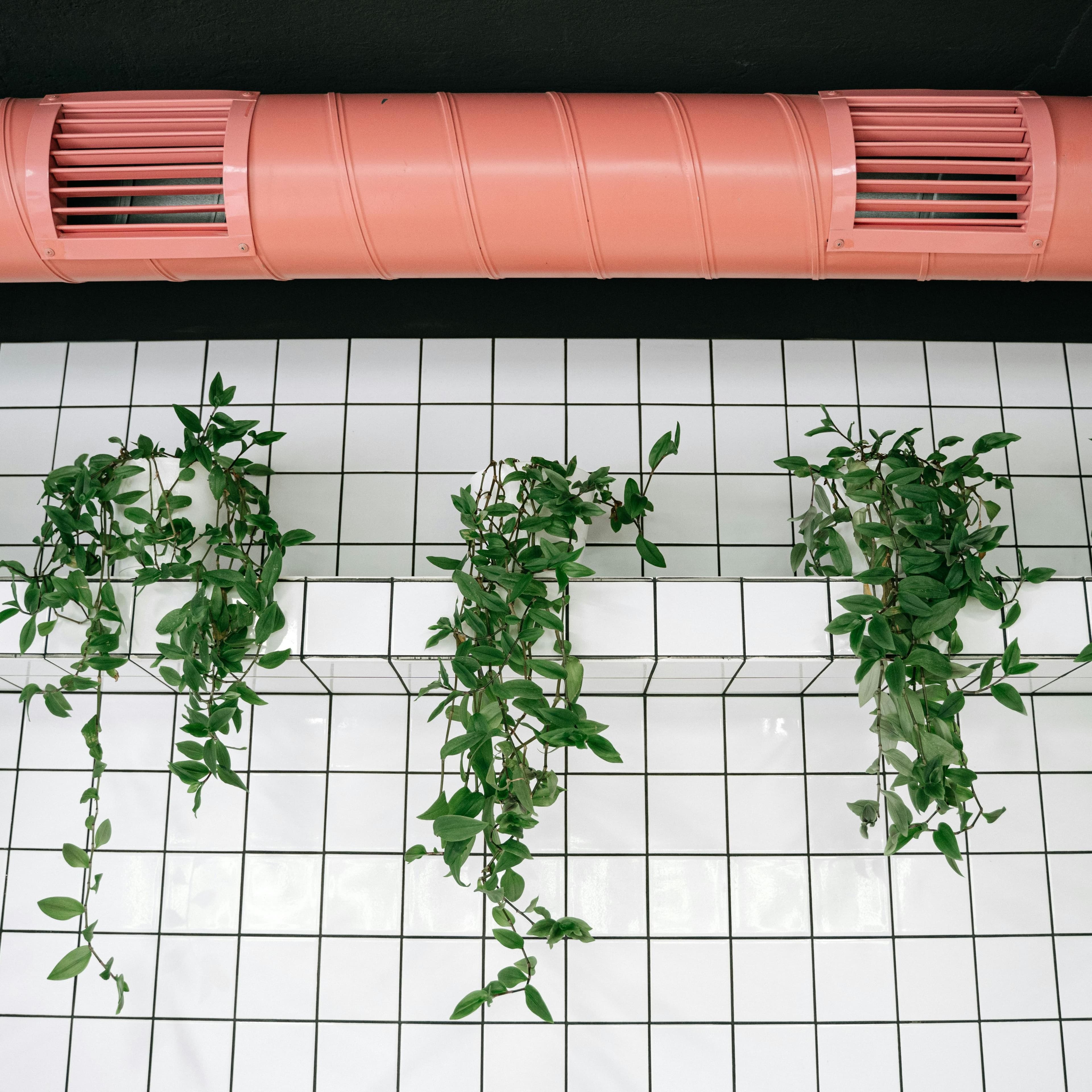
Enhance building energy efficiency through AI automation
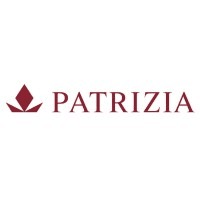
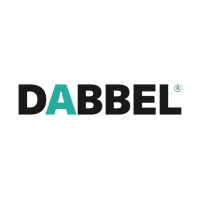
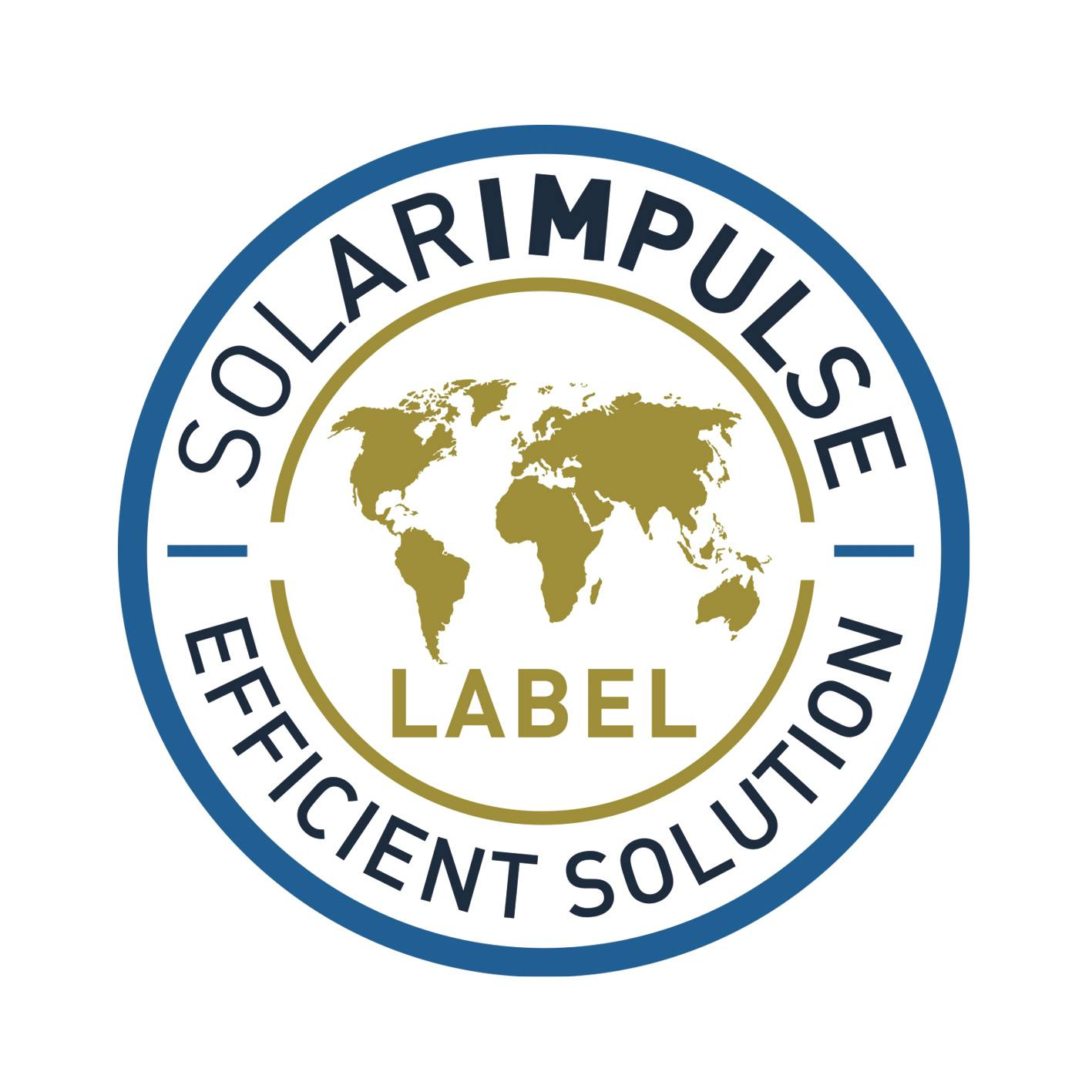
Summary
AI-powered automation solution to optimize the energy efficiency of the HVAC system of a large office complex, resulting in significant energy and cost savings.
Context
This case-study has been developed in partnership with the Solar Impulse Foundation, which is promoting – through assessing, certifying and facilitating access to finance - the multitude of clean and profitable solutions currently available worldwide. Discover more of Solar Impulse Foundation’s labelled solutions here.
PATRIZIA AG, a leading partner of global real assets, manages the Treptower Berlin, an office complex with diverse energy needs. As part of its commitment to environmental, social, and governance (ESG) goals, Patrizia AG sought to reduce the building's energy consumption and carbon footprint. The complex Heating, Ventilation and Air Conditioning (HVAC) system, which includes heating networks, air handling units, cooling towers, and chilled beam operation, presented a significant opportunity for optimization.
Solution
Patrizia AG worked together with DABBEL AI GmbH to implement their automation solution, which leverages artificial intelligence (AI) to optimize the operation of HVAC systems in commercial buildings. The technology collects real-time building data, including sensors, meters, occupancy and weather forecasts. The AI engine then analyzes this data, identifies patterns and inefficiencies, and autonomously adjusts the HVAC system's settings to minimize energy consumption while maintaining optimal comfort levels.
Implemented at Treptower Berlin in March 2022, the solution involved integrating DABBEL's software with the building's existing control systems through a secure Virtual Private Network (VPN) connection. This process requires an existing Building Management System (BMS), ideally with BACnet/IP communication (or other popular protocols), as well as the provision of necessary documents and data points. Once the system was operational, the AI engine began learning the building's energy patterns and adapting its control strategies accordingly.
Following the initial setup, the AI engine continuously monitored and analyzed data from the HVAC systems. This included real-time data on temperature, occupancy, energy usage, and weather conditions. The AI engine then used this data to learn the building's unique energy patterns and identify opportunities for optimization.
Over time, the AI engine refined its control strategies, making automatic adjustments to heating, cooling, and ventilation settings to minimize energy consumption while maintaining occupant comfort.
Impact
Sustainability impact
Climate
This initiative targets Patrizia AG’s scope 1 and 2 emissions.
The initiative led to a 36% reduction in HVAC energy consumption at Treptower Berlin, saving 1,755,781 kWh annually and reducing CO2 emissions (Scope 1 and 2) by 605 tons.
Nature
Reduced Resource Extraction: By improving energy efficiency and reducing overall energy consumption, the AI solution indirectly reduces the demand for fossil fuels and other natural resources used in energy production. This leads to less habitat destruction from mining activities and decreased water usage associated with energy production processes, preserving aquatic ecosystems.
Lower Pollution Levels: Efficient energy management results in fewer emissions of pollutants such as sulfur dioxide (SO2), nitrogen oxides (NOx), and particulate matter, which can have detrimental effects on natural habitats and biodiversity.
Social
Enhanced Indoor Comfort: The AI solution continuously monitors and adjusts HVAC systems to maintain optimal indoor conditions. This provides consistent indoor temperatures, enhancing comfort and productivity for building occupants.
Increased Productivity for Facility Managers: The AI solution automates the control and monitoring of HVAC systems, reducing the need for manual adjustments and oversight. This allows Facility Managers to focus on strategic tasks rather than routine operational duties.
Business impact
Benefits
The 36% reduction in energy consumption resulted in a cost saving of more than €180,000 in 2023. This demonstrates a significant return on investment for the tenant, and the ongoing energy savings will continue to contribute to the building's financial performance. The implementation of the technology also enhances the building's sustainability profile, which can be a valuable asset for attracting and retaining tenants.
Costs
A prerequisite for implementing the AI solution is the Pre-Check, which involves an assessment of the building's existing systems and infrastructure to ensure compatibility and optimal integration. This Pre-Check is a one-time payment of €2500-6500, depending on the building size. Besides this, no further capital expenditure is required as no additional hardware or retrofit is needed. The operational expenditure involves a license fee that is individually calculated based on the building structure, typically around 1€ per m² per year. However, the rapid payback period due to the significant energy savings makes this a financially attractive investment. Every €1 spent on the license fee results in energy cost savings of €2-6.
Impact beyond sustainability and business
Co-benefits
Optimized HVAC systems can improve occupant comfort by adapting to real-time conditions. This can lead to increased productivity and satisfaction for building users.
Potential side-effects
As with any software-based system, there is a potential for unexpected situations, such as an interruption of the connection. The system then reverts to the status quo prior to the implementation of the software. So, if the connection is interrupted, there are no consequences or chaos in the control of the building.
Implementation
Typical business profile
The technology is ideal for commercial buildings with complex HVAC systems and a focus on achieving energy efficiency and sustainability goals. It is particularly suitable for buildings with diverse occupancy patterns and varying energy needs.
Approach
The solution provider has established a site-to-site VPN tunnel between their cloud services and the building to access the BMS network remotely. If the BMS is connected to the internet, the client can establish the VPN connection. If not, the solution provider offers remote assistance to set up the VPN connection using computer software like TeamViewer or by sending pre-configured hardware if necessary.
Once the VPN connection was established, the learning phase began, lasting approximately 7 working days. During this period, the technology has:
Scanned the BACnet network to identify available controllers and data points
Collected and analyzed data from the building
Visualized the data in the technology’s cloud dashboard
Following the learning phase, the control phase spanned another 7 working days. During this period, the technology has:
Confirmed the data points list with the client’s facility managers
Started controlling the HVAC systems
Monitored and reviewed the performance during the initial weeks of implementation
After the initial control phase, the technology continuously monitored and optimized the HVAC systems based on real-time data and ongoing analysis. The system ensured that energy consumption remained within guaranteed thresholds without compromising comfort levels.
Stakeholders involved
Project Leads: Project managers, Asset managers, and technical experts from both DABBEL AI GmbH (the solution provider) and Patrizia AG (the client).
Company Functions: Patrizia AG's facility management, energy management, and sustainability teams were actively involved in the project.
Main Providers: DABBEL AI GmbH (provider of the AI-powered automation solution)
Key parameters to consider
Before implementing the technology, several pre-conditions must be met to ensure a smooth onboarding process. The client must ensure that the building has a centralized Building Management System (BMS) installed, ideally with the main communication protocol BACnet/IP. However, most common protocols are also supported. All necessary data points from the HVAC systems should communicate via BACnet/IP. Required documents such as BMS screenshots, HVAC drawings, HVAC plans, and monthly historical energy consumption data must be provided. A stable internet connection with at least 5 Mbit/s upload/download speed and 99.9% all-year usage time is required. Additionally, a router or firewall supporting IPsec or OpenVPN must be available. If there is no internet connection, the technology can provide a mobile network solution, which may incur additional costs.
Building Complexity: the solution is particularly effective in complex buildings with diverse energy needs and multiple HVAC systems
Data Availability: The quality and quantity of data collected from building systems are crucial for the AI engine's learning and optimization process. Adequate sensors and data collection infrastructure are essential
Integration with Existing Systems: the solution should be compatible with the building's existing building management system (BMS) to ensure seamless integration and control
Regulatory Compliance: Ensure that the implementation of the technology complies with relevant energy efficiency and data privacy regulations
Time indication
The installation and commissioning of the solution typically takes about 2 to 3 weeks, provided all conditions are met. Initially, a site-to-site VPN tunnel is established between the technology’s cloud services and the building to enable remote access to the BMS network. This step generally takes 1-2 days.
Once the VPN connection is established, a learning phase of approximately 7 working days begins, during which the technology scans the BACnet network and collects and analyzes data from the building. Following this, a control phase lasting another 7 working days takes place, where the technology starts controlling the HVAC systems and monitors performance.
The results are noticeable after the first month, at which point the full operation begins.
Implementation and operations tips
Incompatible communication protocols
Challenge: The BMS may not fully communicate via BACnet/IP or other common protocols
Solution: Evaluate and potentially translate other protocols (Modbus RTU, KNX, OPC UA) into BACnet/IP using hardware solutions. Conduct a thorough pre-check of BMS protocols to identify compatibility issues early
Incomplete data point access
Challenge: Not all necessary data points from the HVAC systems may be accessible
Solution: Ensure full access to all required data points. If certain points can't be overwritten by the technology, secure the necessary permissions for read/write access
Manual interference:
Challenge: Manual changes in the BMS can conflict with the technology's automated controls
Solution: Coordinate with facility managers to minimize manual interventions. Educate the operational team on the importance of maintaining automated control for optimal performance
Data quality and availability:
Challenge: Insufficient or poor-quality historical energy consumption data
Solution: Provide detailed and accurate historical data in the required formats. Use additional services, such as remote assistance for collecting BMS screenshots, to ensure data completeness
The DABBEL Pre-Check as an overall prevention method
The DABBEL Pre-Check is an essential preliminary step designed to prevent complications during the AI implementation process. By thoroughly assessing the building’s existing systems and infrastructure, this Pre-Check ensures compatibility and readiness for DABBEL AI integration. It involves verifying the communication protocols, gathering necessary data points, and reviewing required documents such as BMS screenshots and HVAC plans. By identifying potential issues early, the Pre-Check allows for timely resolutions, thereby ensuring a smooth and efficient implementation process. This proactive approach minimizes disruptions, reduces implementation time, and guarantees that the technology operates effectively from the start, leading to optimal energy savings and compliance with regulatory requirements.