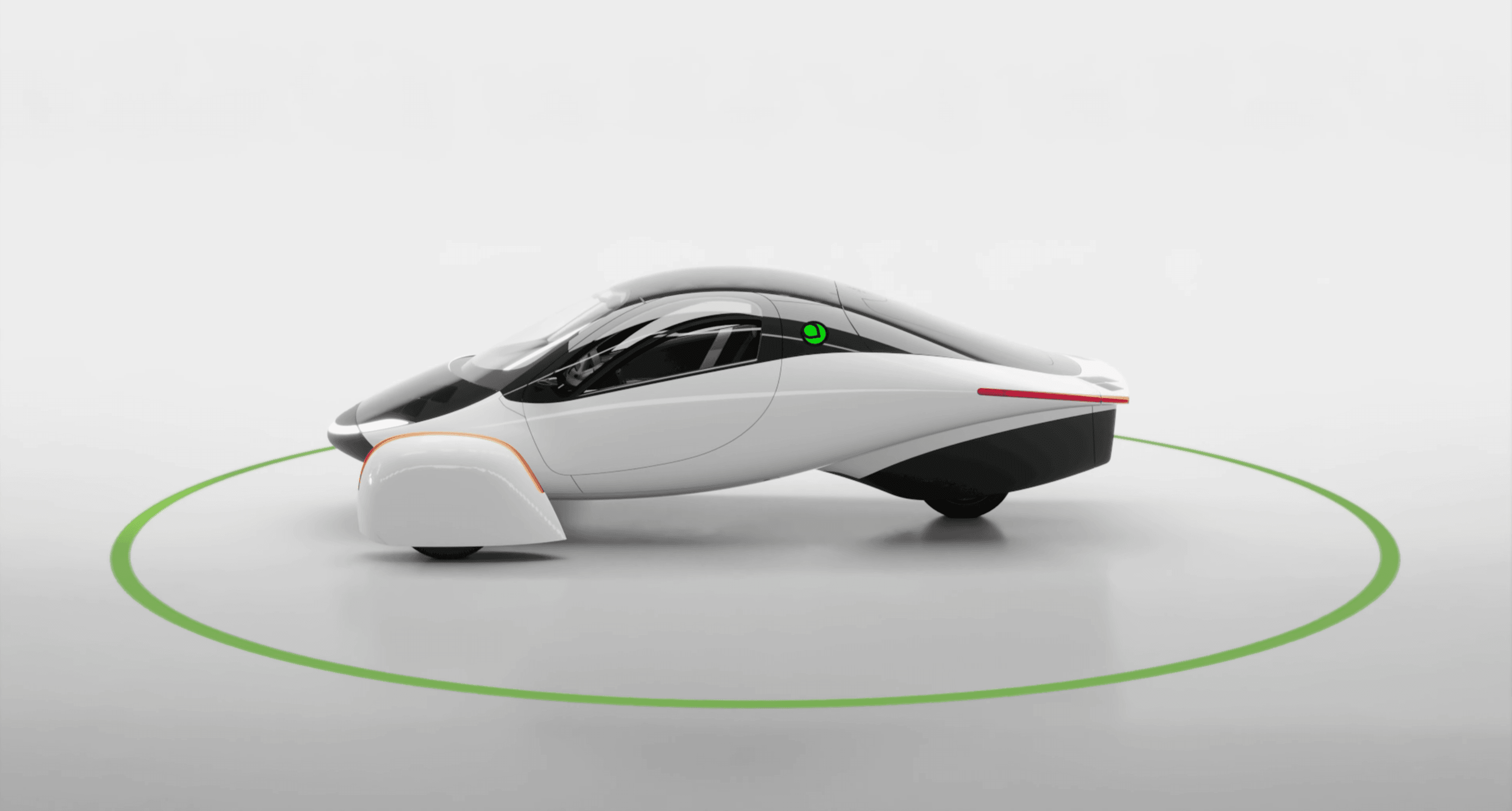
Optimize electric vehicle design to reduce energy use
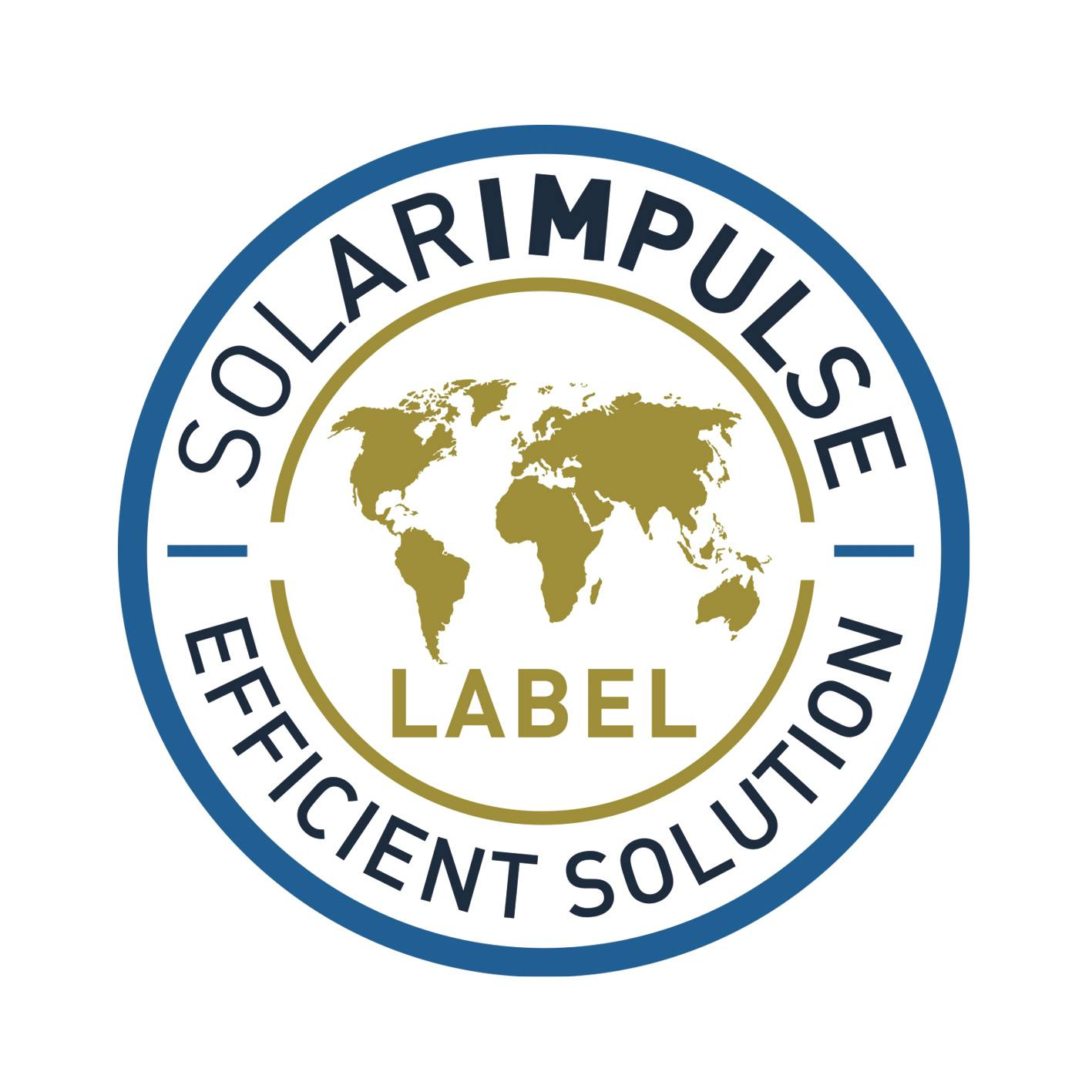
Summary
Aptera Motors collaborated with AirShaper to optimize the aerodynamics of a solar electric vehicle resulting in significant energy efficiency gains and reduced environmental impact.
Context
This case-study has been developed in partnership with the Solar Impulse Foundation, which is promoting – through assessing, certifying and facilitating access to finance - the multitude of clean and profitable solutions currently available worldwide. Discover more of Solar Impulse Foundation’s labelled solutions here.
Aptera Motors, in its pursuit of creating the most efficient electric vehicle, recognized that aerodynamic drag is a major factor in energy consumption, especially at highway speeds. To address this challenge and further enhance the sustainability of the car, the company sought a solution to optimize its vehicle's aerodynamics.
Specific Decarbonization Challenges:
Aerodynamic Drag: One of the primary decarbonization challenges faced by Aptera Motors is reducing aerodynamic drag, which significantly impacts energy efficiency in electric vehicles (EVs). At highway speeds, aerodynamic drag becomes the dominant force resisting the vehicle's motion, leading to higher energy consumption and reduced range.
Energy Efficiency: Enhancing energy efficiency is crucial for reducing the carbon footprint of EVs. Aptera Motors aims to maximize the distance traveled per unit of energy, thereby reducing the overall energy demand and associated emissions from electricity generation.
Material and Manufacturing Footprint: Another challenge is minimizing the environmental impact of vehicle materials and manufacturing processes. This includes using lightweight, sustainable materials that do not compromise the vehicle's strength and safety.
Solar Integration: Integrating solar panels into the vehicle design presents unique challenges in terms of optimizing the surface area for maximum energy capture while maintaining vehicle aesthetics and aerodynamics.
Decarbonization Strategy:
Aerodynamic Optimization: Aptera Motors employs advanced computational fluid dynamics (CFD) simulations and wind tunnel testing to design vehicles with low drag coefficients. The three-wheeled, teardrop shape of Aptera's vehicles significantly reduces aerodynamic drag, making them one of the most efficient EVs on the market.
Lightweight Materials: The company uses lightweight, but strong composite materials for the vehicle body, which not only reduce the overall weight but also enhance the structural integrity and safety of the vehicle. These materials can be recycled up to five times, giving it a low CO2 lifecycle. This approach helps in decreasing energy consumption, increasing range, and lowering the vehicle’s CO2 lifecycle.
Integrated Solar Panels: Aptera incorporates solar panels into the vehicle's body, allowing for additional energy generation directly from sunlight. This solution extends the vehicle's range and reduces reliance on external charging infrastructure, contributing to lower overall emissions.
Solution
Aptera Motors partnered with AirShaper, an innovator in aerodynamic simulation software, to refine the car’s design. AirShaper's software utilized computational fluid dynamics (CFD) and generative design algorithms to automatically explore and evaluate a vast number of design iterations, identifying the most aerodynamically efficient shapes.
Through this collaboration, Aptera Motors achieved a 6% reduction in drag on the Aptera. This significant improvement was achieved through subtle modifications to the vehicle's shape, including the wheel pants, roof structure, and rear wheel fairing. To achieve this, they used AirShaper’s shape optimization tool, which automatically morphs 3D models to improve aerodynamic performance.
Impact
Climate impact
Targeted emissions sources
Scope 2: The increased efficiency extends the car's solar-powered range, reducing the need for grid charging
Scope 3:
Category 1: Reducing the drag also has an indirect benefit, as it reduces the size of the battery for the Aptera. This reduces the impact in terms of resources (rare earth materials) and the emissions associated with it.
Category 11: The reduction in aerodynamic drag reduces the energy demands to drive a vehicle forward. So this results in a direct reduction of required electric energy or fuel doing the use phase of the car.
Decarbonization impact
The 6% reduction in aerodynamic drag translates directly to a 3% reduction in energy consumption from electricity used to charge the car. This translates to lower emissions for every mile driven on grid power. The increased efficiency also extends the car's solar-powered range, reducing the need for grid charging and further lowering Scope 2 emissions.
Nature impact
The reduction in drag reduces the size of the required battery. That results in a direct reduction in the amount of resources needed to produce the car (see above). Also, a lower weight results in a lower tire wear and thus less fine dust particles.
Business impact
Benefits
The collaboration resulted in a more efficient and aerodynamic car, further differentiating it in the market. The increased solar range and reduced battery size enhance the vehicle's appeal to consumers seeking sustainable and cost-effective transportation.
Costs
The project cost for all of the simulations, automated morphing and consultancy was in the order of magnitude of 50.000 USD.
Impact beyond climate and business
Co-benefits
The improved aerodynamics not only enhance efficiency but also contribute to a quieter and more stable ride for car drivers.
Implementation
Typical business profile
Companies in the automotive industry looking to improve aerodynamics[LA1] . Especially for electric vehicles, the need to reduce drag is essential, as this has a direct impact on the battery size. This, in turn, directly impacts the cost, the resources needed and the dynamics of the cars.
Approach
First, Aptera had to upload their 3D model of the vehicle to the AirShaper platform. Then, they set up the basics, like the velocity, rotating wheels and radiators. For a full optimization (where the software will automatically morph the shape to reduce drag) they also had to define a 3D design space within which the software is allowed to morph the design. Aptera worked on 6 areas for this morphing: the nose, belly, roof, front wheel covers, rear wheel cover and the tail.
The entire procedure from upload to finished simulation is automated and runs on HPC (high performance infrastructure) to deliver results fast. No experience in simulations is required and consultancy through AirShaper was available to help interpret results and improve the design.
Aptera used the outcomes of the generative design tool to come up with new shapes to further cut the drag coefficient of their car.
Stakeholders involved
Project Leads: Aptera Motors co-CEOs
Company Functions: Engineering, design, marketing, sales
Main Providers: AirShaper (aerodynamic simulation software)
Other: Suppliers of lightweight materials, battery technology, and solar panels
Implementation and operations tips
Optimizing the aerodynamics of a vehicle is something which is best done during the early stages of design. At that point, there is still a lot of room left for design changes which can have a large impact on the aerodynamics. Later on, as the design gets more detailed and ultimately frozen, it’s harder to make significant gains in aerodynamics.
Additionally, you need to be able and willing to work with cloud solutions. For various companies, this is still a concern. But adoption of cloud solutions in general is on the rise.
A few of the challenges Aptera faced, and their solutions:
1. Aerodynamic Efficiency:
Challenge: Achieving an ultra-low drag coefficient to maximize energy efficiency was a significant technical challenge. The unique teardrop shape required extensive testing and iteration to balance aerodynamics with practical design considerations.
Solution: Aptera employed advanced computational fluid dynamics (CFD) simulations and extensive wind tunnel testing to refine the vehicle's shape. This iterative process ensured that every aspect of the design contributed to reducing drag while maintaining vehicle stability and aesthetics.
2. Lightweight Materials:
Challenge: Developing a vehicle body that is both lightweight and strong posed material engineering challenges. Traditional materials either added too much weight or lacked the necessary durability.
Solution: Aptera utilized advanced composite materials, specifically carbon fiber and fiberglass, which offered the perfect balance of strength and lightness. These materials were chosen for their performance and sustainability, resulting in a durable yet lightweight vehicle body.
3. Solar Panel Integration:
Challenge: Integrating solar panels into the vehicle's surface without compromising aerodynamics or aesthetics was a complex challenge. Ensuring efficient energy capture while maintaining the vehicle's sleek design required Aptera to invent automotive grade two-axis curved solar panels.
Solution: Aptera's engineering team designed custom, flexible, and highly efficient solar panels that seamlessly integrate into the vehicle's body. These panels are optimized for maximum energy capture and minimal impact on aerodynamics, providing additional range through solar energy.