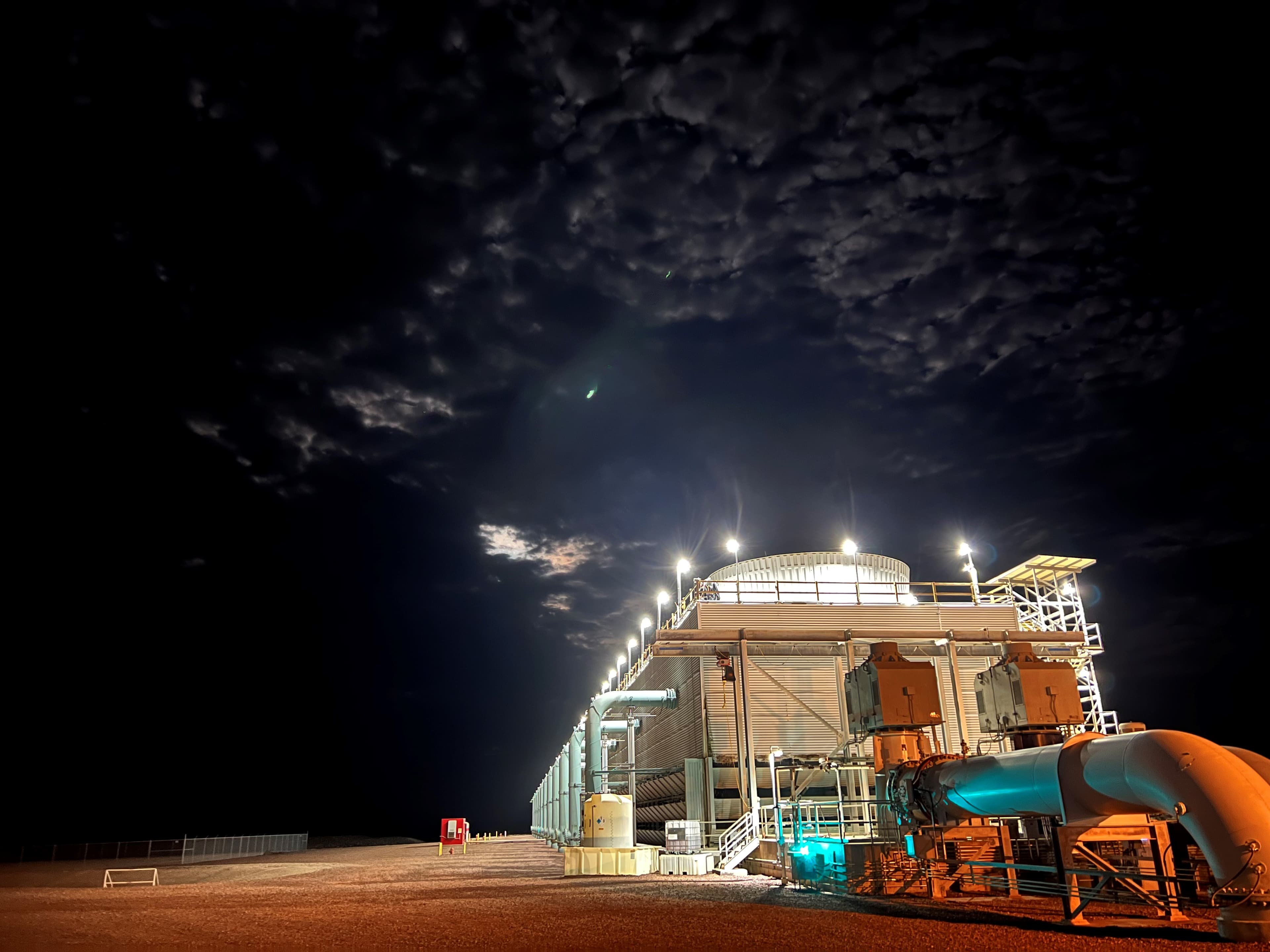
Optimize lubricant application in industrial turbines
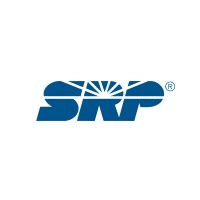
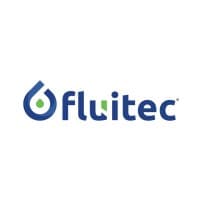
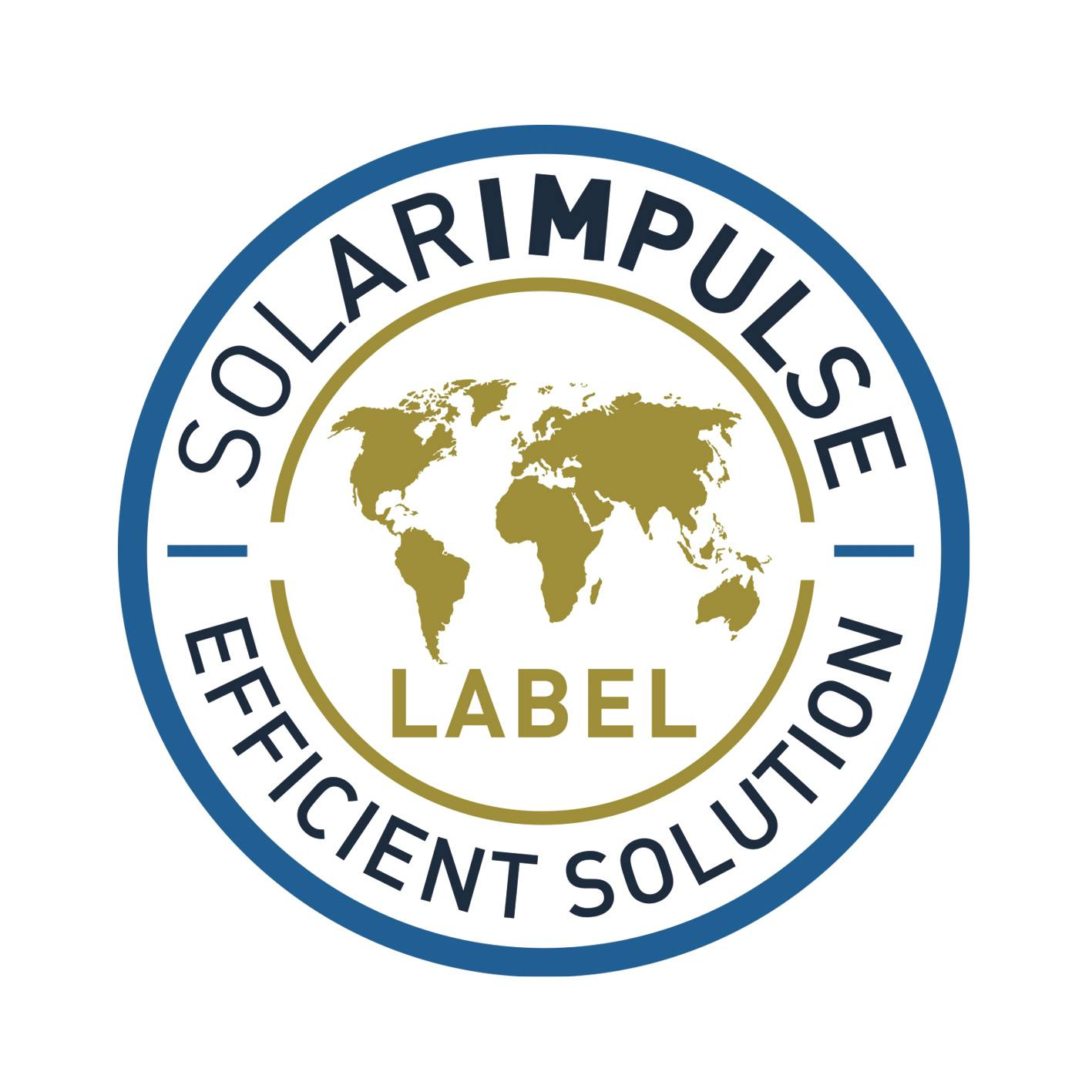
Summary
SRP, a major US power utility, partnered with Fluitec to transform their consumable turbine oils into lubricants that will last the life of their turbines, reducing costs and CO2e
Context
This case-study has been developed in partnership with the Solar Impulse Foundation, which is promoting – through assessing, certifying and facilitating access to finance - the multitude of clean and profitable solutions currently available worldwide. Discover more of Solar Impulse Foundation’s labelled solutions here.
SRP (Salt River Project), a public power utility in the United States, provides reliable and affordable electricity and water to over two million people in central Arizona. As part of its commitment to sustainable operations, SRP recognized the need to address the issue of premature oil degradation in its combined-cycle power plants. Traditional oil management practices involved frequent oil changes, which not only incurred significant costs but also contributed to environmental pollution through the production, transportation, and disposal of new lubricating oil. This case study took place at SRP’s Mesquite Power plant in Arlington, Arizona. It is a 1250MW combined cycle power plant.
Solution
SRP partnered with Fluitec to implement the Fill4Life™ program, a comprehensive solution that enables a "fill for life" strategy for lubricants. This approach involves:
Contaminant Removal
Fluitec's technology filters out harmful particles, water, and other contaminants that contribute to oil degradation.
Component Replenishment
Essential additives and solubilizers are replenished to maintain the lubricant's optimal performance and protective properties.
Continuous Monitoring
Online and offline oil analysis is conducted to monitor lubricant health and identify potential issues before they escalate.
By continuously maintaining and optimizing the condition of the lubricant, the program eliminates the need for frequent oil changes, extending the lifespan of lubricants and reducing waste.
Impact
Sustainability impact
Climate
Targeted emissions sources
Scope 1: This initiative directly targets emissions from SRP's power generation operations.
Decarbonization impact
By extending the lifespan of turbine oil beyond 300% of the industry standard, SRP has avoided the production, transportation, and disposal of over 50,000 gallons (~ 190,000 liters) of oil per decade per turbine. This has resulted in a significant reduction of approximately 150 tons of CO2e (carbon dioxide equivalent) emissions per year per turbine.
Nature
There are approximately 200 million gallons of used oil in the US that are improperly disposed of each year. SRP’s efforts ensure that none of their used turbine oils contribute to this total.
Business impact
Benefits
The implementation of the program has yielded substantial financial benefits for SRP’s Mesquite Power. By optimizing oil life and preventing associated costs with oil changes, Mesquite Power realizes over $275,000 per year in OPEX savings (Operating Expenses) and over 150 tons per year in CO2e emissions. Furthermore, less human interaction with their turbine oil translates to a safer working environment for their employees.
Costs
Investment costs are lower than the cost of one oil change, so savings are realized immediately.
Implementation
Typical business profile
This solution is applicable to any industrial facility operating small to large machinery that relies on lubricating oil and hydraulics. Power generation plants, general manufacturing, chemical plants and other industries with similar equipment can benefit from this technology. The savings realized in this case study are similar to any other power plant in the world operating with steam or gas turbines.
Approach
Assessment: Fluitec conducted a comprehensive oil analysis to assess the condition of SRP's turbine oil and determine the feasibility of implementing the Fill4Life™ program
Implementation: Fluitec installed the necessary filtration, oil rebalancing additives and monitoring equipment, tailored a maintenance plan for SRP's specific needs, and provided training to SRP personnel on the operation and maintenance of the system
Monitoring and Maintenance: SRP, with ongoing support from Fluitec, continues to monitor the oil condition through routine analysis, ensuring the continued effectiveness of the Fill4Life™ program and proactively addressing any potential issues
Stakeholders involved
Project Leads: Operations and Maintenance team at SRP, the solution provider’s technical experts
Company Functions: Operations, Maintenance, Engineering
Main Provider: Fluitec
Key parameters to consider
Oil Condition: A comprehensive oil analysis is essential to determine the suitability of the Fill4Life™ program and establish a baseline for monitoring progress
Equipment Compatibility: Ensure that the Fill4Life™ technology is compatible with the specific lubricants and equipment used in the facility
Operational Conditions: Consider the operating environment and contamination levels, which can impact the effectiveness of the program
Implementation and operations tips
Early Adoption: Implement the Fill4Life™ program early in the equipment's lifecycle to maximize the potential benefits in terms of oil life extension and cost savings
Regular Monitoring: Adhere to the recommended oil analysis schedule to proactively identify and address any potential issues
Partnership: Foster a close working relationship with the solution provider to leverage their expertise and optimize the results of the program