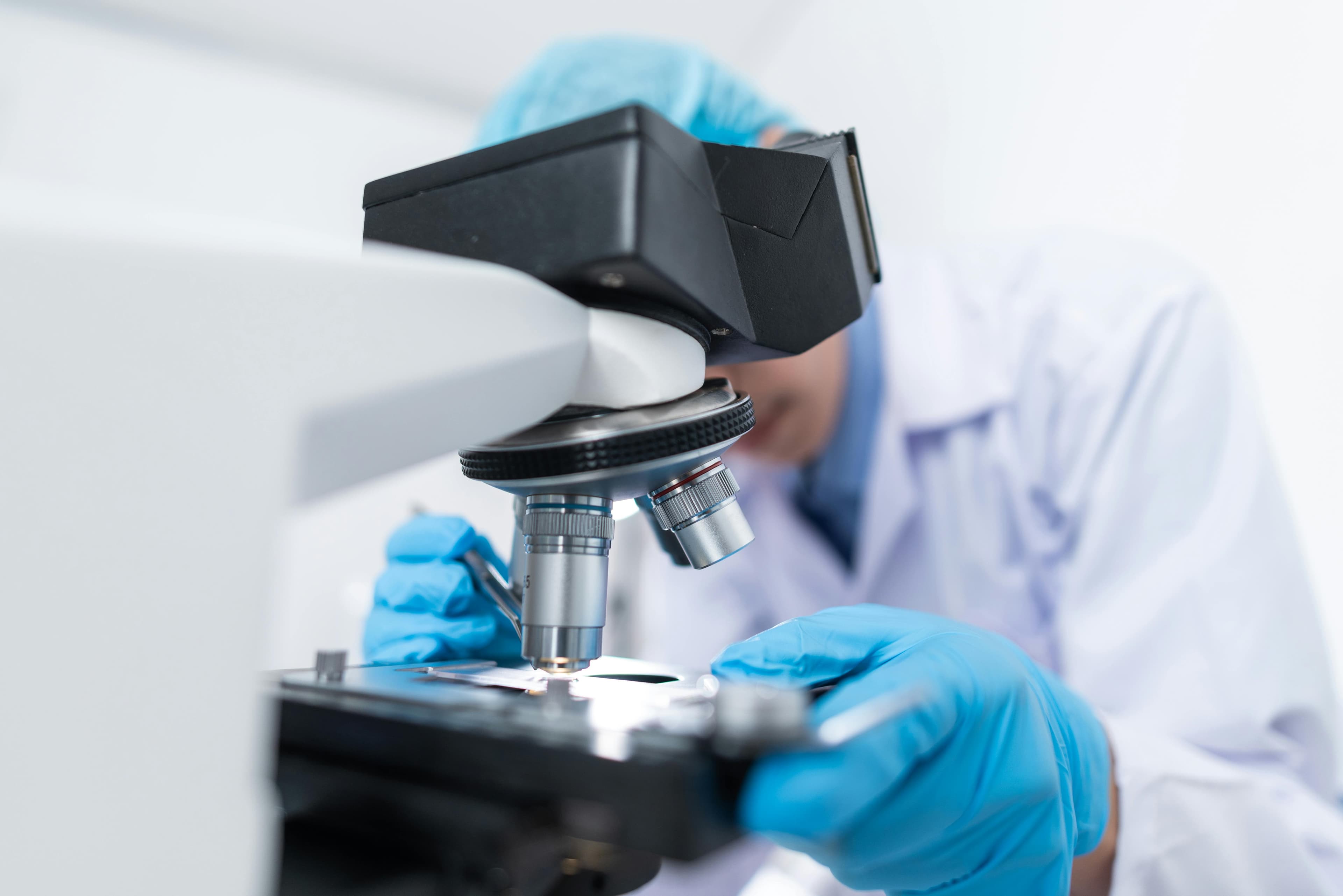
Optimize solvent recycling and recovery
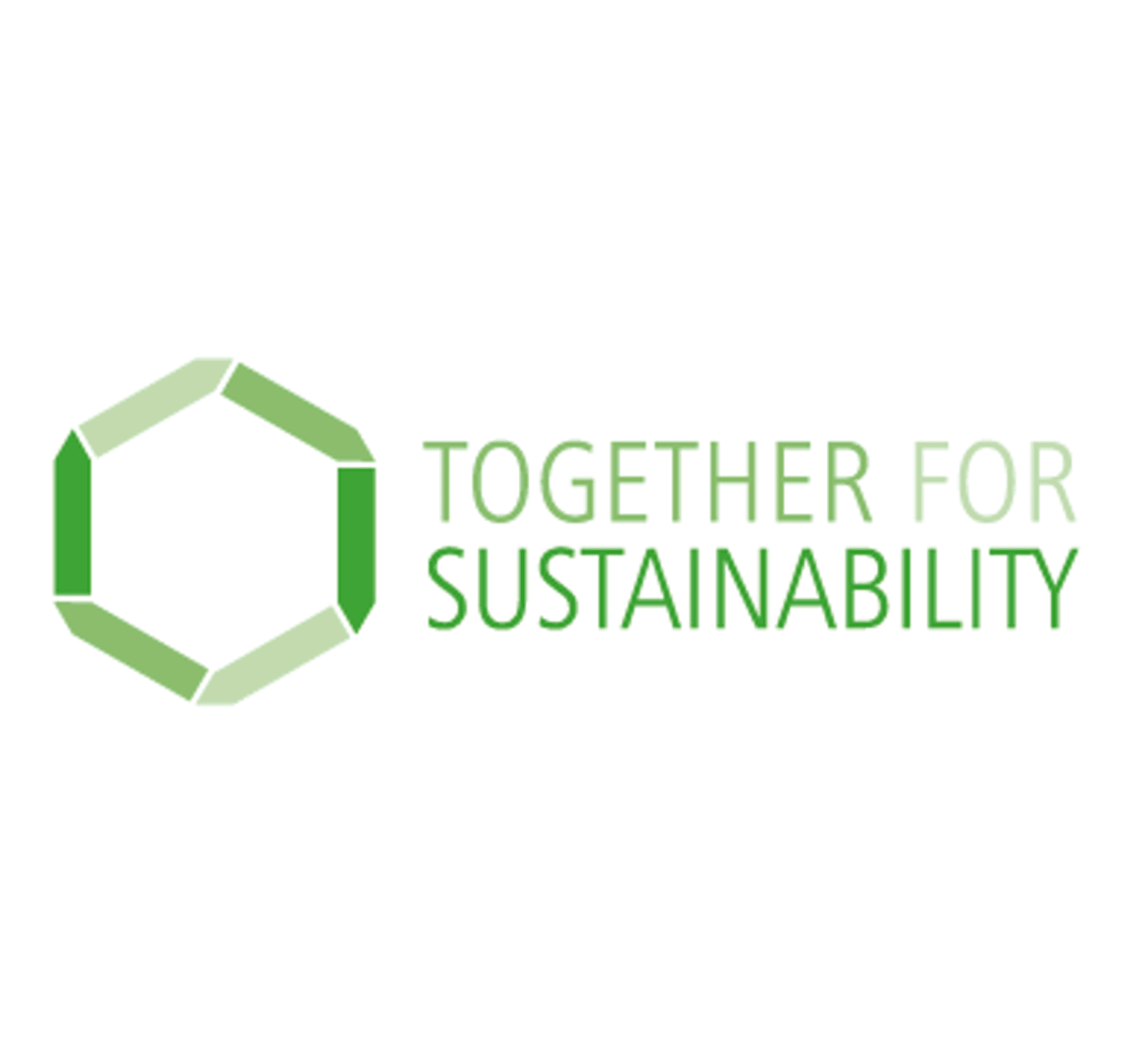
Summary
Solvent recovery and recycling initiative significantly reduces carbon emissions and promotes sustainable processes in pharmaceutical manufacturing.
Context
This case study has been developed in partnership with Together for Sustainability (TfS), an industry-leading initiative driven by chemical procurement specialists, dedicated to building sustainable chemical supply chains.
As sustainability becomes a key focus across the pharmaceutical industry, companies are looking for manufacturing partners that can develop their products efficiently while minimizing their environmental footprint. In line with its commitment to transparency and its Vision ZERO —which aims to reduce emissions, raw material consumption, and waste—Lonza introduced this approach. The Active Pharmaceutical Ingredient (API) production process in Lonza’s Small Molecules Division requires large amounts of solvents, resulting in significant waste streams. A typical API production process begins by dissolving reactants in a strong solvent, followed by switching to a weaker solvent where the final product crystallizes, is isolated through filtration, and washed to obtain the pure API. This process will typically generate 50 to 100 tons of waste per one ton of pure product. Historically, it was common to incinerate all waste, and thus produce significant CO2 emissions. However, Lonza is now focusing on recovering and recycling solvents from these waste streams wherever possible. In 2022, 30% of solvents used in Lonza’s Small Molecules Division were recycled, and this figure increased to 35% in 2023. Of this, 20% was reused in the API process, while the remaining 15% was sold for reuse in other non-pharmaceutical industries.
Solution
In 2023, Lonza’s Small Molecules Division implemented solvent recovery strategies and technologies, leading to substantial CO2 reductions. As a result, 35% of all solvents used in the division’s production process in Switzerland were recycled, with the goal of reaching 70% solvent reuse in the future
Lonza's Small Molecules Division approach to solvent recovery is interdisciplinary, involving teams from Production; Manufacturing, Science, and Technology (MSAT); Process Technology and Innovation (PTI); Environmental Health and Safety (EHS), and Waste Management. Lonza considers points such as the technical evaluation, business case, lab feasibility, and any development and implementation issues that might arise. Additionally, the company takes into account recycling concerns such as quality assurance, customer approval for reusing solvents in the process, or identifying other customers interested in purchasing solvents for reuse.
These are the product development phases:
Technical evaluation: Different technologies are evaluated either for sub-streams or for the mixtures of all waste streams in a given process. The process development evaluation phase is conducted using Solvent Recovery Database, CHEMCAD and CCD (Physical Property Database).
Lab feasibility: The next step is to test the feasibility through lab experiments, which involve one liter batch rectification and Lab-scale pervaporation. These tests provide the foundation for a technology evaluation on paper.
Business case: Based on the lab results, a business case is developed, which is the last milestone prior to development and implementation. The business case also includes an energy and CO2 balance to assess environmental benefits.
Development and implementation in plant: Most solvents are recovered through distillation or a hybrid process involving distillation. The flexibility of batch distillation provides a solution to most solvent recovery challenges. These are the most common used technologies:
Fine Chemical Complex (FCC): 10 Distillation columns
Solvent Recovery Plant: 7 distillations Columns
Large Scale Pervaporation
Impact
Sustainability Impact
Climate
Scope 1
Scope 1 refers to direct emissions caused by waste incineration; this is the CO2 released from the smokestack during incineration. In 2022, Lonza reduced CO2 emissions by around 19,000 tons through solvent recycling processes in its Small Molecules division, and in 2023, this reduction increased to more than 20,000 tons (i).
Scope 2
All electricity used at Lonza sites where this project is conducted comes from renewable sources, thus Scope 2 is not relevant.
Scope 3
On average, solvents contribute around 2.5 tons of CO2 per ton (of solvent) to Scope 3 emissions. In 2022, Lonza saved around 19,000 tons of Scope 3 emissions, and in 2023, this figure raised to more than 20,900 tons.
Nature
Reduced waste going through incineration, thus lowering emissions of volatile organic compounds (VOCs) by capturing process off-gas in a closed system.
Recycling/Recovery of Solvents reduces solvent production and resource extraction, thus lowering the environmental impact of those industries. Recycling avoids the production of fresh solvents.
Business Impact
Benefits
Approximately 10,000 tons of recovered solvent were recycled back into the API process or sold for reuse in other non-pharmaceutical industries.
Costs
The investment required includes the cost of state-of-the-art recovery and waste treatment facilities, infrastructure such as modern heat, insulation, efficient HVAC, heat recovery, green electricity, and circular utility economy.
Operating costs are minimized by treating waste in the most sustainable way possible and reworking solvents to be reused in the same processes or in other industries.
Impact beyond climate and business
Potential side-effects
Recycling solvents into the API process is difficult because of Good Manufacturing Practice (GMP), regulatory constraints, and customer approval.
(i) Scope 1 reduction is slightly lower that it could be given emissions resulting from the energy recovery process.
Implementation
Typical business profile
This initiative is most relevant for pharmaceutical companies, especially those involved in API production processes that require large amounts of solvents.
Approach
Step 1: Simulation tools can predict the yield and purity of recovered solvent from a waste stream which can then be used to design a laboratory distillation trial and aid in the industrial scale-up process. From the laboratory, valuable information can be obtained such as the impurity profile, potential fouling, foaming, or precipitation phenomena. Additionally, other information is gained such as samples needed for thermal safety or corrosion investigations and generate material for the recycling tests required to recycle the API into the final process.
Step 2: Scaled up for industrial-scale production facilities, including large-scale manufacturing facility known as the Fine Chemical Complex (FCC). In the FCC, Lonza has 10 distillation columns that can be used to recycle solvents within the API production processes, as well as a dedicated solvent recovery plant with seven additional distillation columns used to recover solvents for reuse outside of Lonza. Additional technologies such as pervaporation are also available.
Step 3: Managing waste streams from API production offers several options. In 2023, 65% of the solvents were incinerated and the other 35% were recycled or reused in different processes.
The least sustainable option is shipping the waste off-site for incineration, which would be necessary if solvents aren’t recycled, due to limited on-site incineration capacity.
The most sustainable option is to recycle the solvents back into their original process. In 2023, this was done with 20% of the solvent waste.
However, there are several options in between:
Recycling solvents into the API process is challenging because of current good manufacturing practices (cGMP), regulatory constraints, and the need for customer approval. As an alternative, Lonza has a large network of customers interested in purchasing these solvents for different applications, which accounted for 15% of solvent waste.
Energy generated by waste can be recovered through the incinerator, which can be used to produce steam and reduce the amount of natural gas needed otherwise. This method was used for 15% of solvent waste.
Stakeholders involved
Production: Implementing solvent recovery processes in manufacturing
Manufacturing, Science, and Technology (MSAT): Providing technical support and ensuring process efficiency.
Process Technology and Innovation (PTI): Developing innovative technologies for solvent recovery.
Environmental Health and Safety (EHS): Ensuring environmental health and safety compliance.
Waste management: Managing waste streams and optimizing solvent recovery.
Key parameters to consider
Technical considerations, maturity, stakeholders buy-in, and regulatory constraints are key parameters to consider when understanding whether this initiative is relevant for other businesses. Among the technical considerations these are the most relevant: yield and purity of recovered solvent, impurity profile, potential fouling, foaming, or precipitation phenomena. Samples are also needed for thermal safety or corrosion investigations and generate material for the recycling tests required to recycle the API into the final process.
In terms of timeframes, the solvent recovery process from the simulation to the implementation takes around four months, while integrating the recycling process into a GMP API process requires at least one year.
Implementation and operations tips
To reach its goals, Lonza focuses on four key aspects: facilities, equipment, and utilities; production processes and changeover; waste treatment rework and recycling; and culture and behavior. Having access to state-of-the-art infrastructure that encompasses modern heat; insulation; efficient heating, ventilation, and air conditioning (HVAC); heat recovery; green electricity; and circular utility economy is vital.
To establish sustainable production procedures, Lonza has implemented smart process development. to increase yield and reduce solvent usage, lowering the overall mass effectiveness. When waste is generated, it is treated in the most sustainable way possible, with solvents reworked for reuse in the same processes or repurposed for other industries. Finally, to further enhance employee culture, long-term sustainability goals (SDGs) are linked to incentive plans. Employees are provided with information and training to foster idea generation and promote sustainable practices. This approach aims to encourage employees to adopt environmentally friendly behaviors in both their work and personal lives.
To address challenges, ensure success, and drive wide-scale adoption, it is critical to share resources and strategies to reduce the negative environmental impact of pharmaceutical manufacturing. By providing ongoing training and support, Lonza encourages employees to generate and implement new ideas.