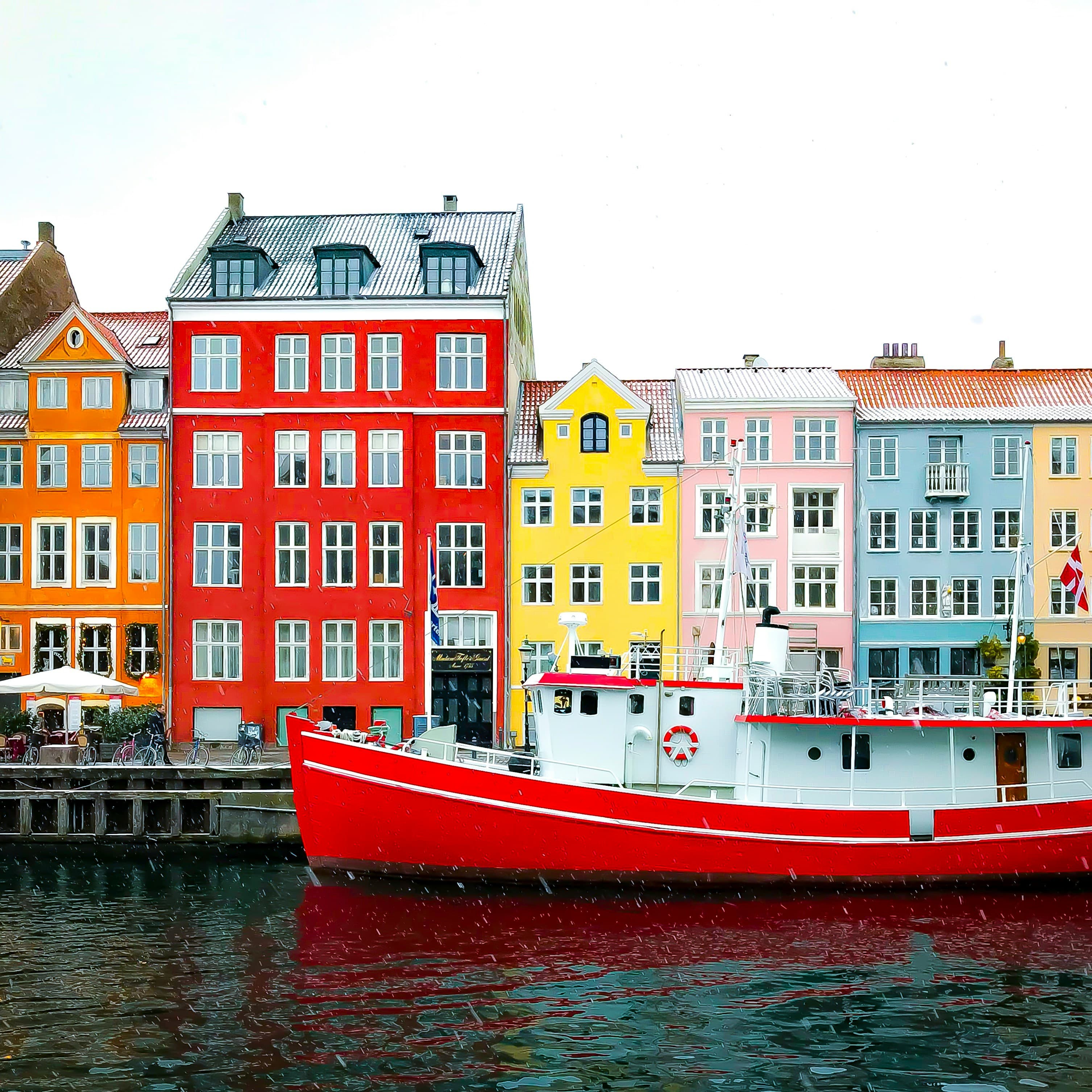
Re-use excess energy from operations to heat buildings
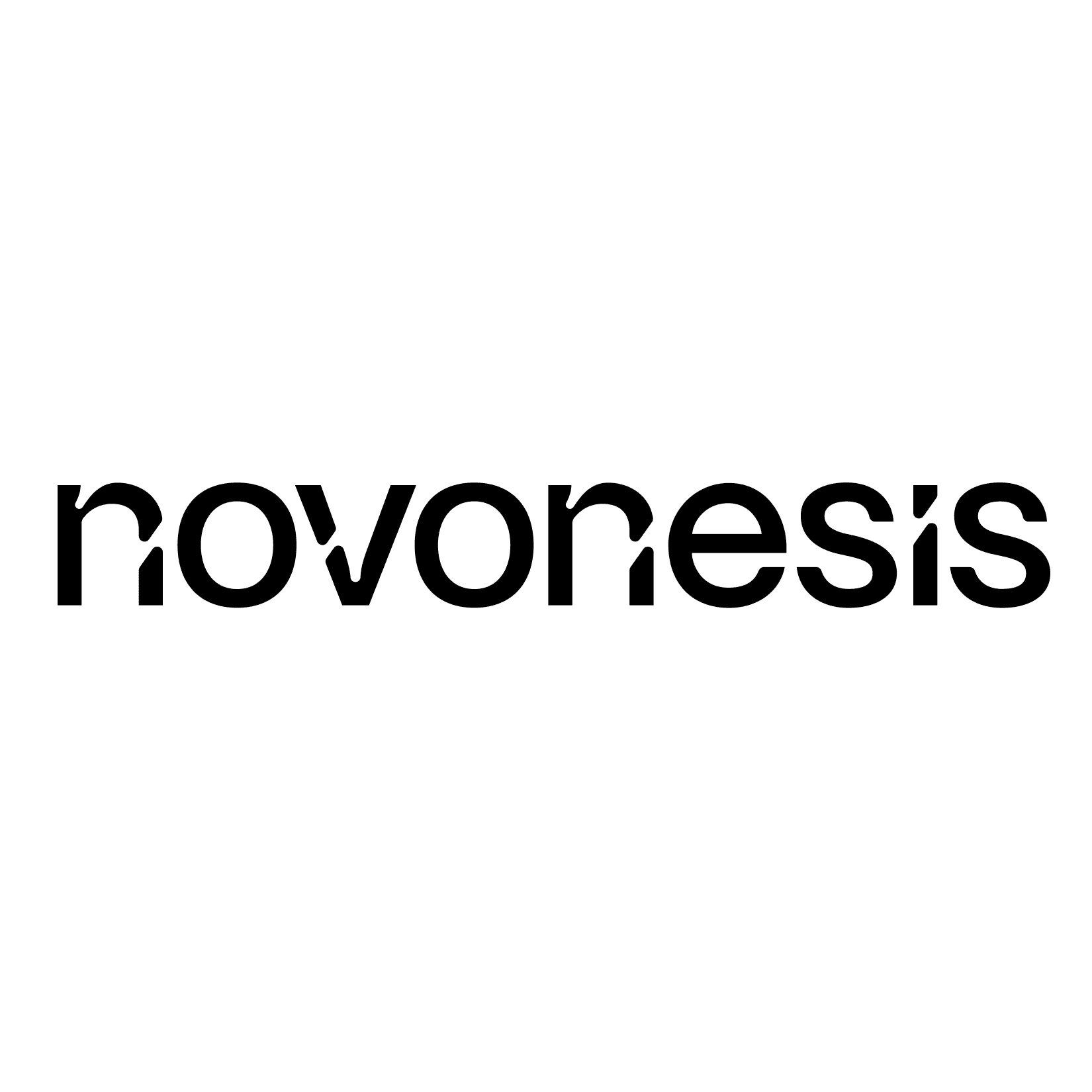
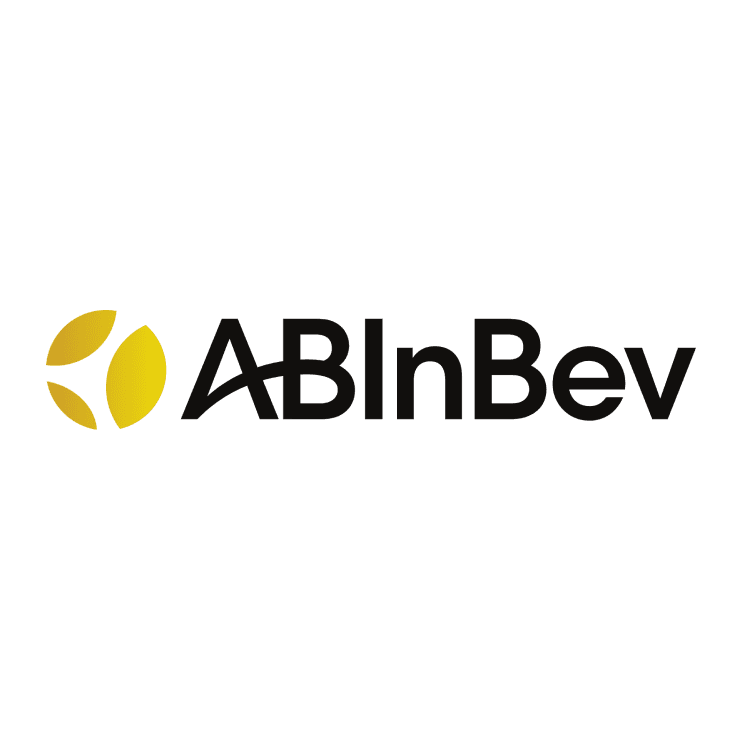
Summary
Novonesis uses captured energy from operations to heat homes through a district heating system in Greater Copenhagen.
Context
This case study is part of decarbonization best practices shared with AB InBev Eclipse sustainability program’s community. Discover more about the Eclipse program here.
Novonesis is a major company globally in biological solutions, producing a wide range of industrial enzymes and microorganisms. As part of its Science Based Target, the company has committed to reducing Scope 1 and 2 GHG emissions by 75% by 2030 on a path toward net-zero carbon emissions by 2050. A significant challenge to meeting the target is how to reduce thermal energy losses. In 2019 Novonesis (then Novozymes) initiated a cooperation with HOFOR, the Greater Copenhagen Utility, about utilizing Novonesis’ excess heat in the HOFOR’s district heating network. HOFOR supplies district heating (DH) to approximately 670,000 customers in Copenhagen. HOFOR wants to have a competitive and CO2-neutral DH supply. Both companies have a green strategy where energy efficiency is part of the efforts to reduce the companies’ CO2 emissions.
Following the success in Copenhagen, in 2020 a decision was made to establish cooling system using sea water for Novo Nordisk and Novonesis’ joint production site in Kalundborg as part of the first phase to collect heat for distribution in the Municipality of Kalundborg and neighboring Hoelbaek. The project will be fully in place by end of 2025.
Solution
Copenhagen Energy Capture
In 2019 Novonesis partnered with HOFOR the local utility company in Copenhagen to capture excess heat from the fermentation facility and distribute it to households through district heating. The cooperation resulted in the planning and installation of a heat pump, with a heat production capacity of 4 MW, that started operation at the end of 2020. The heat pump uses excess heat from Novonesis’ enzyme production and supplies about 2,000 local citizens in Copenhagen with district heating. The heat pump has reduced HOFOR’s use of natural gas, oil, and biomass for district heating, and contributed to a more diverse energy- and technology mix. Furthermore, the heat pump has reduced the consumption of water and electricity in Novonesis’ cooling towers because the heat pump produces cooling to Novonesis while providing heat to HOFOR’s district heating network.
Kalundborg Energy Capture
Today, the excess heat from the production in Kalundborg is not used, so Novo Nordisk and Novonesis will establish a new cooling system, which will supply district cooling to the respective factories in Kalundborg. In 2025, Kalundborg Forsyning's district cooling and heating center will deliver a cooling effect of up to 166 MW. The technology behind the plant draws seawater from nearby Kalundborg harbor and replaces a current cooling that uses fresh surface water. The system has the added advantage of not needing any chemicals. The plant can collect enough surplus heat to potentially heat more than 40,000 households.
Impact
Sustainability impact
Climate
Scope 1 In Novonesis production site in Fuglebakken, Copenhagen the annual reduction in CO2 was estimated to be up to 2,000 tons per year. The figure reduces CO2 from an already low baseline due to the relatively low carbon energy sources used for HOFOR district heating in Copenhagen. The district heating project in the Kalundborg site is in the first phase but the expected the impact on CO2 emissions will be significantly larger since the scale in the of the Kalundborg project will deliver cooling about more than 40 times greater than the HOFOR project.
Nature
In the Novonesis Fuglebakken site the heat pump saves energy and water from cooling towers. For the site in Kalundborg, the new system will use sea water for cooling and reduce the need to draw fresh surface water from nearby lake Tisso. The water saving from the district cooling project in Kalundborg is 300.000 m3/yr.
Social
These district heating projects create a direct benefit to the local community as well as supporting the energy independence of a region reliant on natural gas from neighboring countries.
By investing in recovering excess heat and working with the utility, HOFOR, it was possible to distribute heat to over 2000 homes in Denmark.
The surplus heat generated from the project in Kalundborg can potentially heat more than 40,000 households.
Business impact
Benefits
Heat pump usage in Novonesis is necessary for cooling the fermenters and maintaining the efficiency of the system. Investing in these systems ensures the long term ability to meet increasing demand from customers while achieving the GHG emissions targets. The cooperation resulted in the planning and installation of a heat pump, with a heat production capacity of 4 MW, that started operation at the end of 2020. The heat pump uses excess heat from Novonesis’ enzyme production and supplies about 2,000 local citizens in Copenhagen with district heating.
Costs
For the HOFOR project, the cost of establishing the heat pump was approximately €4.6 million. At the time of the final investment decision, the simple payback time of the heat pump was estimated to be 8 years. In addition to reduced costs, the heat pump contributes to a more diverse energy and technology mix since it reduces natural gas- and oil-based district heating production, and to some extent also substitutes biomass-based district heating production.
Cost for the Kalundborg system will entail creating a district cooling systems. The initial investment in Kalundborg is €188 million.
Indicative abatement cost
Potential side-effects
The compressors for heat pumps create noise and since the Fuglebakken plant is near residential Copenhagen it necessitated a building that had good sound insulation.
Implementation
Typical business profile
Companies that have manufacturing processes with surplus heat that can be transferred for use in another process.
Approach
Steps for implementation
Quantify the amount of excess heat in your system and how much it varies. The technical solution depends very much on this
Identify a system capable of absorbing the excess heat and map the requirements (hour by hour, month by month) in order to understand the business case. I.e., it can be difficult to sell excess heat in the summertime. Best options are system requiring heat steadily throughout the year
Investigate the technical solution along with your business partner (if external) to find the most cost effective solution
Discuss in detail the potential variation in excess and required heat to elucidate whether or not the business case holds
Make sure no regulations might provide a barrier to the project (anything from selling heat, to generated noise and storage of cooling agent)
Apply for funding and execute the project
Stakeholders involved
Internal Stakeholders involved
The project was the result of collaboration between these departments:
Sourcing
Engineering
Sustainability
Finance
Legal
External Stakeholders involved
Novonesis' Fuglebakken site partnered with the Greater Copenhagen Utility (HOFOR).
In the site in Kalundborg the project involved a joint investment with Novonesis’ sister company, Novo Nordisk, and was a collaboration with the Kalunborg Symbiosis which is a public private partnership that includes 17 organizations including the municipality of Kalundborg. All parties in the symbiosis are invited to participate in the district heating project which is modular and built to accommodate new members as necessary. Buy-in from private land owners was also needed.
Key parameters to consider
Heat pumps can be noisy necessitating significant noise insulation. They also require system monitoring to regulate fluctuations in temperature.
Cooling towers are an open system that can collect debris from the outside necessitating in installation of filters to the heat pump.
However, the technology including construction, operations, cost and maintenance were well understood. Expected life span of the project is 20 years. District heating infrastructure was already in place in Copenhagen, making it possible to use the heat in the community.
For Kalundborg and neighboring Hoelbaek, the infrastructure is to be built and necessary for the capture and distribution of heat. This will involve the solicitation of additional participants and can be built in stages and expanded as demand increases.
There are technical constraints using salt water in an industrial environment. This is not new technology but using it at a large scale can be challenging.