
Recycle polyurethane reactor in refrigeration industry
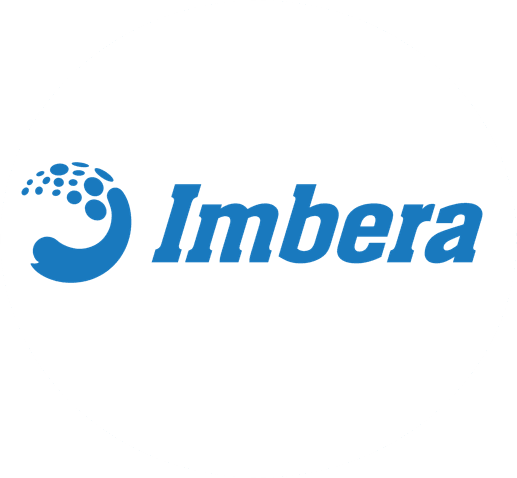
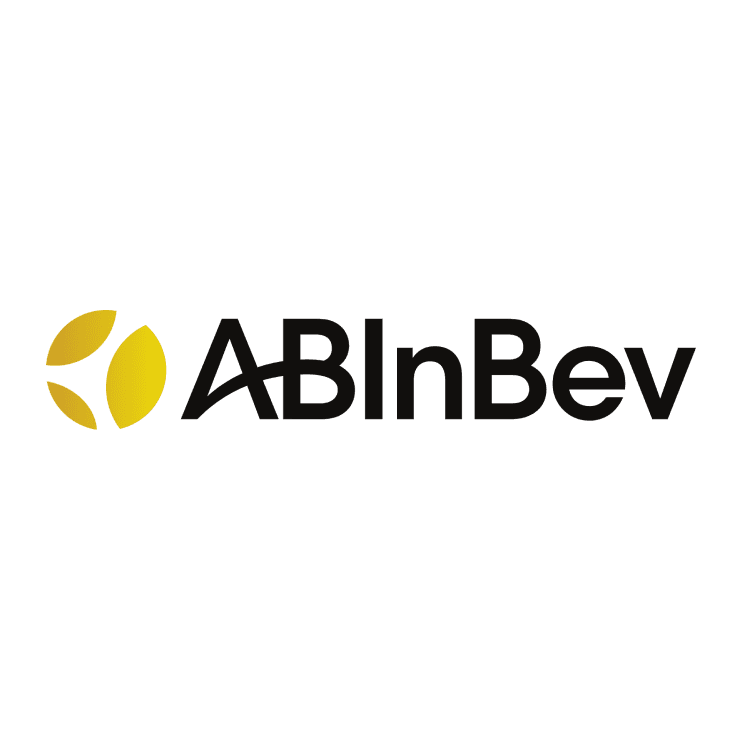
Summary
Imbera/EOS implemented a reactor that can chemically process up to 400 tons of waste polyurethane from old coolers, and transformed it into recycled raw material for new coolers.
Context
This case study is part of decarbonization best practices shared with AB InBev Eclipse sustainability program’s community. Discover more about the Eclipse program here.
Imbera, a refrigeration company based in Mexico, implemented a new type of polyurethane reactor leading to significant emissions reduction and cost reduction.
Imbera's sustainability strategy considers a wide environmental and social strategy. Within Environmental pillar there are the following targets: Net Zero emissions by 2050 (Scope 1+2+3), Zero Waste Facility by 2030 (Mexico), and 100% Circular Product design by 2030. To achieve this objective, Imbera applies a circular economy strategy through all the lifecycle of the product.
One of the main challenges is Rigid Polyurethane (PU), which is one of the key elements of the cooler (it provides structure and insulation). Nonetheless, is the most critical material of the product regarding final disposition, because worldwide almost 50% of this waste is going to landfill, and the rest is incinerated, due the lack of infrastructure to recycle this material. As a consequence, all the commercial PU available to date for coolers is made with 100% virgin material. Both factors affects the environment by increasing waste, polluting soils, and generating Green House Gases, which contains toxic fumes that affects human health and biodiversity.

Solution
Imbera has developed a synergy with every part of the value chain to recover old coolers, in a final disposition facility that is currently recovering components and materials that are mainly closed loop.
In 2024, the reactor arrived, and it started to transform old polyurethane into recycled polyol, which is one raw material to produce polyurethane.
An investment of USD 3,835,000 was made on this German technology to be able to chemically process the polyurethane, through glycolisis. This is the first reactor in America and the second worldwide. Imbera is going to be the first in the industry to use recycled polyol on coolers.
A video (with commentary in Spanish) and some images are included to illustrate the process.



Impact
Sustainability impact
Climate
With this solution the company and its clients (such as AB InBev) are reducing Scope 3 emissions (raw material and final disposition), with full potential of 1,968 tons CO2e yearly.
Explanation: The reactor on its full capacity can process up to 404 tons/11,244 cubic meters of waste yearly. Nowadays processing this waste implies transport and incineration with a carbon footprint emission equivalent to 1,421 ton CO2e*. With this process, these emissions are avoided.
Furthermore, 910 tons of recycled polyol can be produced yearly. Create this raw material from virgin sources (as usual) can generate a carbon footprint of 3,552 tons of CO2e*, meanwhile first calculations approach estimates that the reactor will generate this material with 3,005 tons CO2e** emissions. That is a 15% reduction of carbon footprint.
Apart from GHG, some old polyurethane can contain gases which are ozone depleting, which are controlled substances now because they cause much damage to the environment. With the technology these gases are contained and properly destroyed.
Notes:
*For this calculations secondary data was used from EcoInvent 3.9 and 3.10 and the use of the software Sima Pro
**For this calculation primary data was used and the software Sima Pro
Nature
Worldwide, almost 50% of this waste is going to landfill. Furthermore, a great amount of air contained inside foam cells can provide oxygen for deep-seated fires and impede efforts to extinguish flames. Another hazard related to landfill fires is toxic fume.
The other worldwide available method is energy recovery, which leads to 99% volume reduction. Nonetheless, this method is not flawless, especially as more and more and more polyurethane foams contain flame-retardants, applied to increase users’ safety. Those additives make it difficult, or even impossible, to carry out energy recovery. Furthermore, when high temperatures are applied PU foams can release toxic compounds and carcinogens, such as carbon monoxide, hydrogen cyanide and nitrogen oxides.
Then this solution will reduce all the soil use and pollution and avoid the generation of GHG and toxic gases.
Social
This project helps to avoid human health and environmental impacts caused by dumping or open burning of polyurethane waste, particularly for people on vulnerable situation living near open dumping or landfills.
Explanation: when landfill in polyurethane the gases generated by the combustion include isocyanates, which are compounds with high toxicity. Exposure to them can lead to skin, eyes and respiratory system irritation. The last one can be so strong that even 0.02 ppm exposition can lead to so-called isocyanate asthma. Higher levels can cause pneumothorax. Polyurethanes show much higher toxicity during thermal degradation under aerobic conditions.
Business impact
Benefits
With this project many parts of the value chain can benefit from sustainable innovations that position the company with a competitive advantage against other producers.
The current method of final disposition for some countries with middle income is landfilling. With this final disposition huge amounts of material is exposed which affects the environment and brand reputation.
Before the reactor the material have no economic value, and for its destruction by incinerating it was necessary to pay for transport and destruction. Now this cost can be avoided and transformed into a valuable product with a competitive economic value on the market.
Costs
The reactor cost was USD 3,835,000 and was paid with capital from the company. No external subsidies applied
The reactor investment is going to be recovered long term with the sell of the polyurethane
For a short term the facility is obtaining some significant operative cost reductions (specific information is confidential)
Indicative abatement cost
The investment will be recovered by selling and internally using polyol recycled obtained.
Co-benefits
With this initiative it is expected to:
Prove to stakeholders that a significant change can be achieved with sustainability innovations
Generate green jobs
Serve as an example for other companies to implement disruptive solutions
Expand the culture of sustainability
Continue developing the inclusion strategy
Implementation
Typical business profile
This initiative is relevant for polyurethane users (construction, cooler manufactures, cool rooms industry, plastics, chemical producers, cars manufactures, etc), and for the beverage and food industry.
The reactor is mainly focused for industries in Mexico, but can be extended with a higher cost to the USA and near countries in Latin and South America.
Approach
The old polyurethane is obtained from old coolers from beverage and food industry, but it can be easily extended to all the users of polyurethane.
The reactor is located in Queretaro, Mexico.
The recycled polyol generated can be mixed with virgin polyol from 20% to 80% for different products, including cooling manufacture.
Step-by-step approach:
Initiation: When the company and its clients recognized the negative environmental impact of waste polyurethane, they decided to create a facility specialized in the disassembly of coolers. After conducting research, they determined that the most environmentally responsible method available was co-processing polyurethane. This process eliminates 99% of waste volume and prevents the release of toxic fumes. Since the facility's inception, this co-processing method has been effectively implemented. However, it is the most expensive part of the final disposition process, which causes the overall strategy for final disposal to be costlier than standard disposal methods.
Solution: To ensure this material retains its environmental and economic value, various reuse options were explored but later discarded. Recycling emerged as the necessary step forward. Subsequent research was conducted to identify different recycling technologies worldwide, leading to the discovery of Reactor solution.
Evaluation: Given the significant investment required, the project team and the board of directors carefully analyzed the technology and the business case. Suppliers, manufacturers, plastic specialists, clients, and various internal multidisciplinary areas were involved in assessing the technical, economic, social, and environmental impacts. A project plan for pre-testing the technology was implemented, yielding successful results. This was followed by a second plan for implementation, and the business case was developed. Ultimately, it was determined that the benefits justified the investment of USD 3,835,000.
After approval: A multidisciplinary team was tasked with implementing the project. This team managed activities such as reviewing contracts, coordinating logistics, preparing the operational team, processing necessary administrative documents with the government, adapting facilities, and coordinating the supply chain for materials, to mention some.
Stakeholders involved
Internal Stakeholders involved
This project was developed with many internal resources including mainly the departments of: R&D, sourcing, sustainability, circular economy, engineering team, final disposition experts, operations, project manager, finance and accountability, quality, and the direction board.
External Stakeholders involved
External involved are: reactor seller, 3 polyurethane suppliers, and 5 polyurethane users of different industries.
Key parameters to consider
This is (as per current knowledge) the second reactor worldwide to process rigid polyurethane, and as such is considered to be a disruptive technology. Significant tests have been conducted before the investment, since 2021 when the idea was first discussed.
By 2023, approvals tests finished and the investment was approved. As of November 2024, the material was already in production.
Implementation and operations tips
Nowadays, half of the capacity of the reactor is feasible due the quantity of material available. The complicated part is that, as this is not a mandatory disposal yet, possibly the clients who properly dispose the coolers or polyurethane products will have to cover logistics to make sure that their polyurethane is properly disposed. To overcome this challenge, extended responsibility is promoted, included in the sell of coolers.