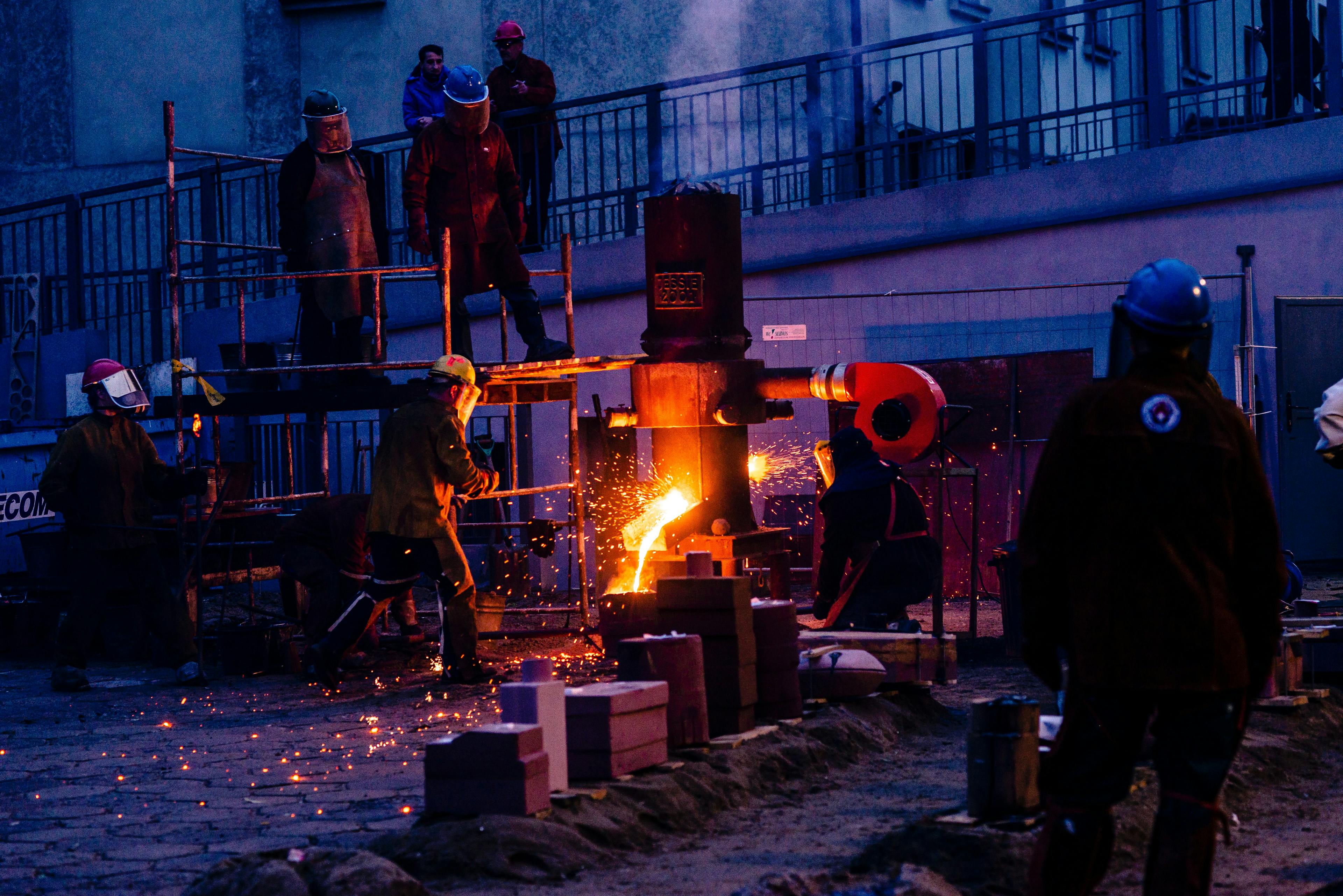
Shift from gas or coal to electric industrial furnaces
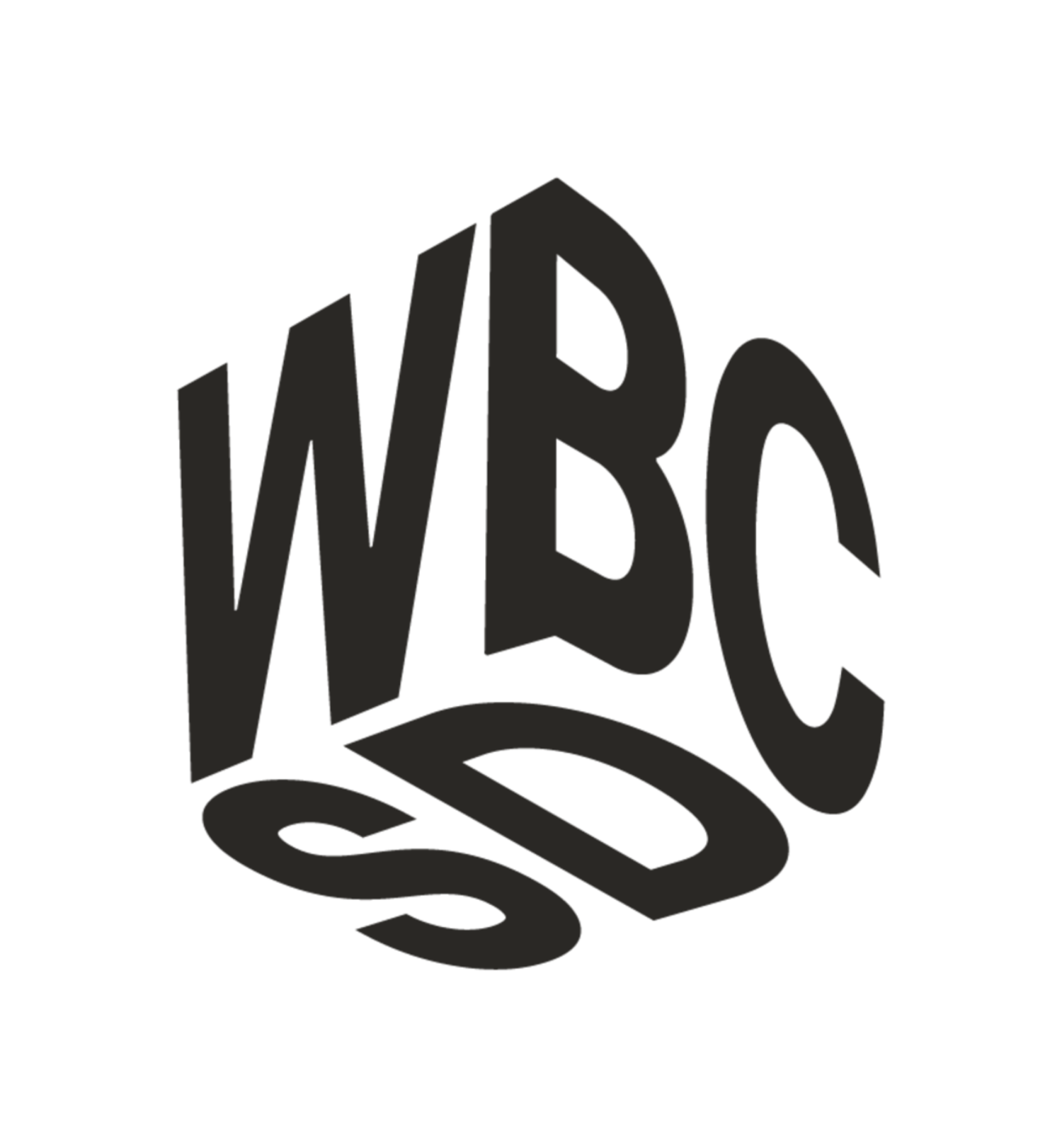
Summary
The decreased cost of electrical equipment and increased energy efficiency grows opportunites for electrictrifying industries, enabling a reduction in GHG emissions
Key resources
Solution
Heat accounts for roughly 38% of energy-related carbon dioxide emissions as it is still largely generated using fossil fuels. In industry, modern renewable energy sources cover only around 12% of the heat consumption (1).
Industrial heat demand by temperature type divides as follows – low temperature (below 100°C), at 15% medium temperature (100 to 400°C) at 30% and high temperature (above 400°C) at 55%. Net Zero Scenario (by International Energy Agency) requires renewable heat consumption in industry to expand by double by 2030 from 2020 capacity levels of 11 EJ to 22 EJ (2). Renewable heat generation capacity must be doubled over the next decade to meet growing industry demand.
The electrification of industry processes is required to further decarbonize emissions related to long-term manufacturing. The decreasing cost of electrical equipment (e.g. industrial electric furnaces) and steadily increasing energy efficiency grows market competitiveness of electric solution for industry-specific applications. In 2017, fuel consumption for energy production in industry accounted for around 45% of energy consumption – which was technologically possible to electrify by 2020 (3).
Image: Industrial energy consumption

Source: McKinsey. Plugging in: What electrification can do for industry
Usage
Electric industrial furnaces with heat demand up to 1,000°C (and over in some instances) are technologically feasible, but not commercially available for all applications. Industry players are constantly developing and testing full-scale electrified solutions in processes such as steam reforming and cracking (in the petrochemical industry), melting in glass furnaces, the reheating of slab in hot strip mill, and calcination of limestone for cement production. The electrification of high temperature heat furnaces would potentially require changes in heat exchangers that capture residual heat.
Industrial electrified furnaces required similar levels capital investment and in 2020, offered similar efficiency levels when compared to conventional, fossil fuels based alternatives – therefore financial savings of electrification are dependent on the cost of electric energy to operate the equipment and conventional fuel prices.
In 2020, electricity in most locations was more expensive per joule than conventional energy or heat sources. For buildings and transport sector electric equipment, efficiency enables life cycle savings on energy costs, making up for higher costs of equipment and higher per-joule price of electricity.
The synergy of renewable sources for electricity generation in country power generation mixes and the electrification of heat generation systems in industrial processes allow industry players to lower their operational costs and greenhouse gas emissions.
Companies aiming to adopt electrified industrial furnaces typically consider the installation of electric industrial furnaces. These are usually companies interested in decarbonization or processes where rapid heating capabilities are needed.
Image: Low electricity prices, or a signicant CO price, increase the nancial attractiveness of electrication

Source: McKinsey. Plugging in: What electrification can do for industry
Impact
Climate impact
Targeted emissions sources
Industrial electric furnaces target carbon dioxide emissions on Scope 1, Scope 2 and Scope 3 with focus in:
Category 1 (Purchased goods and services)
Category 3 (Fuel- and energy-related activities not included in Scope 1 or Scope 2)
Category 10 (Processing of sold products)
Category 12 (End-of-life treatment of sold products)
Decarbonization impact
The use of electric industrial furnaces leads to either the abatement or increase of carbon dioxide emissions. In regions with a high share of renewables within their electricity grids, a maximum of up to 90% reduction of CO2 emissions is possible, compared to current levels. Case-specific decarbonization potential must be analyzed, as levels of environmental impact differ globally, leading to an increase of CO2 emissions, where grid electricity is heavily coal-based.
Emissions from capital investment into electric industrial furnaces and end-of-life carbon dioxide emissions are hard to recognize – due to installation complexity and differences between manufacturers of equipment, as well as recyclability possibilities for designed infrastructure.
Business impact
Benefits
Potential to lower greenhouse-gas (GHG) emissions, increased employee safety, lower infrastructure complexity, lower operating noise.
Costs
Impact on operating costs
Operational cost for electric industrial furnaces through their dependance on electricity prices will result in an increase of cost from 30 up to 300%.
Investment required
Capital investment cost for electric industrial furnaces is like other conventional heating solutions across the implementation of multiple processes. Industry players should assess the cost of installation on a case-by-case basis.
Eventual subsidies used
Regional and country-specific subsidies apply based on location of use.
Indicative abatement cost
Abatement cost for electric industrial furnaces (dependent on technology currently in use):
$US80 to 140/tCO2e
Impact beyond climate and business
Co-benefits
Local lower carbon dioxide emissions, increased air quality in industry zones, lower local noise levels.
Potential side-effects
Possibility of increased total carbon dioxide emissions (dependent on available regional power generation mix).
Implementation
Typical business profile
All industry clients in few selected sectors (e.g. petrochemical, glass, or cement production) interested in electrification of industrial furnaces from 400 to up and over 1000°C (e.g. steam reforming or cracking).
Approach
The installation approach for electric industrial furnaces must be analyzed on a case-by-case basis, with relevant specialists and professionals, as investment and operational costs will vary between processes and regions. The implementation of electrified furnaces might require infrastructure adaptation e.g. for heat exchanges responsible for capturing residual heat.
Key parameters to consider
Solution maturity: in development, only reaching financial feasibility in few selected applications
Lifetime: 15-20 years
Technical constraints or pre-requisites: cost of installation, weather-dependency, local electricity (or heat generation) cost
Additional specificities (e.g., geographical, sector or regulation): regional power generation mix/share of renewables in electricity generation
Implementation and operations tips
The adoption of electrified industrial furnaces enables industry players to reduce their carbon dioxide emissions and maximize the environmental potential of solutions in the long term, if they are supplied with a high share of renewables electricity. Financial feasibility must be analyzed for every implementation, as cost competitiveness might not be reached with current market offerings. In the future, electrified furnaces may offer increased energy efficiency and lower the cost of capital investment or operations.
Going further
Main sources
Further readings