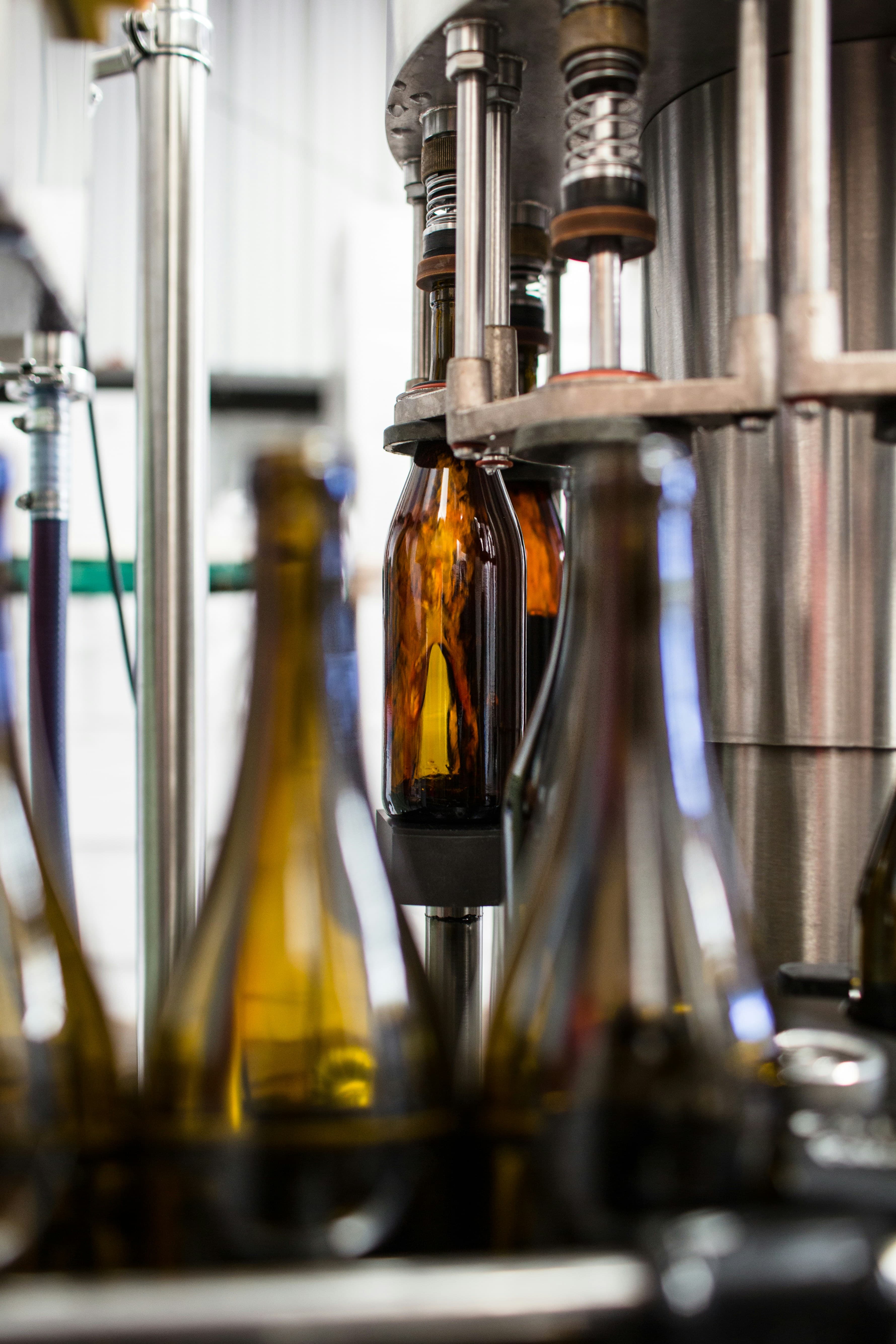
Switch to regenerative furnace system in glass production
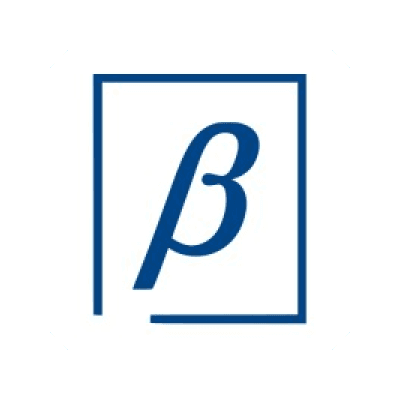
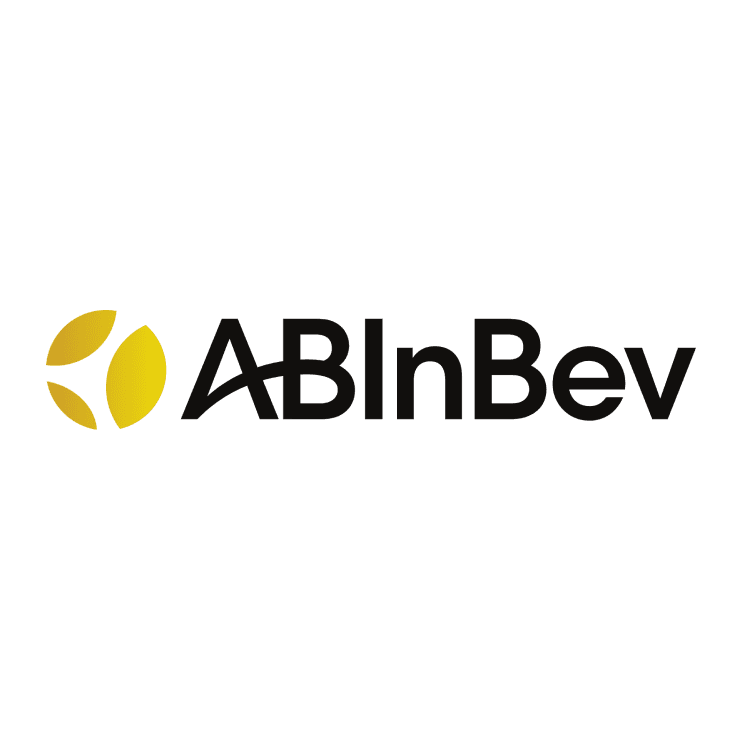
Summary
Beta Glass PLC has implemented a regenerative heat technology and electricity boost system to reduce energy intensity by 8% using less energy to melt a ton of glass.
Context
This case study is part of decarbonization best practices shared with AB InBev Eclipse sustainability program’s community. Discover more about the Eclipse program here.
Beta Glass PLC is a glass production company based in Nigeria, and a member of the Frigoglass Group. Beta Glass faces several key challenges in its journey to decarbonize glass production, primarily due to the energy-intensive nature of furnace operations. Glass production requires continuous high temperature heating, traditionally fueled by natural gas or fossil fuels, which leads to significant CO2 emissions per ton of glass melt. With rising regulatory pressures, natural gas shortages and global commitments to reduce carbon footprints, Beta Glass must also meet industry standards for sustainable production while maintaining operational efficiency.
Another challenge lies in managing resource limitations and infrastructure upgrades to incorporate more sustainable energy sources. Transitioning from fossil fuel-based energy to cleaner alternatives, like electricity or renewables, involves high upfront capital costs and technological integration, particularly in older furnaces. Additionally, the company faces the challenge of scaling up the use of cullet (recycled glass) in production, which requires extensive supply chain adjustments to ensure a consistent and high-quality cullet supply for energy efficiency gains.
Solution
Objective
Beta Glass PLC aims to achieve an 8% reduction in energy intensity by implementing advanced technologies and enhancing operational practices within its glass manufacturing processes.
For this project, the following steps were taken:
Assess furnace compatibility: Check to confirm the existing furnace design and operational parameters to ensure compatibility with hybrid technology
Procure technology: Source the regeneration fans and electrodes from certified suppliers, ensuring they meet operational and efficiency standards. The project partner was BDF
Industries S.p.A., a company in glass engineering, renewable energy and industrial automation.
Furnace shutdown and preparation: Schedule and execute a controlled shutdown of the furnace. Carryout inspections and cleaning to prepare for the rebuild
Install regeneration fans: Integrate regeneration fans into the furnace system to improve heat recovery and pre-heating efficiency
Install electrodes: Position and connect the electrodes at the furnace bottom and sides to provide electrical boosts, reducing fuel consumption
Test and calibrate: Perform initial tests to ensure proper functioning of the installed components and calibrate them for optimal performance
Train personnel: Trained in-house operators and maintenance teams on the operation and upkeep of the hybrid system
Commission for operations: Restart the furnace with the hybrid system in place and monitor performance closely during initial operations
Impact
Sustainability impact
Climate
Scope 1 Emissions: These emissions originate from fuel combustion within the company’s operations, such as the energy-intensive glass melting process. By implementing regenerative technology and electric boost systems, Beta Glass PLC reduces the consumption of fossil fuels, resulting in lower direct emissions of carbon dioxide (CO2) and other greenhouse gases. This action is essential for lowering the company’s overall carbon footprint and aligning with climate goals. The initiative is projected to yield significant climate benefits in terms of GHG reductions. For example, by enhancing energy efficiency, Beta Glass PLC has achieved a 67.3 kg reduction in CO2 emissions per ton of glass produced, translating to a 10.5% decrease in emissions from an initial 520 kg (about 1146.4lb) CO2/ton to approximately 452.7 kg CO2/ton.
Nature
This reduction equates to the environmental benefit of planting nearly 240,000 trees or removing over 1,100 cars from the road each year.
Social
By decreasing greenhouse gas emissions and improving air quality, the company enhances public health, reducing respiratory issues associated with pollution. The shift to renewable energy sources not only mitigates climate change but also fosters economic opportunities through increased recycling efforts, generating jobs and promoting local entrepreneurship. Additionally, community engagement initiatives, such as partnerships with local recycling entities, raise awareness about sustainability, encouraging eco-friendly practices. Through these efforts, Beta Glass PLC not only contributes to a healthier environment but also enriches the quality of life for local residents, demonstrating the powerful role businesses can play in driving social and environmental progress.
Business impact
Benefits
Optimizing energy efficiency sources, the company has achieved substantial reductions in energy costs, leading to significant savings that can be reinvested into further innovation and growth. Improved operational efficiency, evidenced by increased production cycle times from 75% to 93%, not only enhances productivity but also boosts employee morale as workers engage in a more dynamic and productive environment. The adoption of these technologies not only streamlines processes but also reduces downtime, facilitating higher output and improved product quality.
Costs
The sustainability initiative is projected to significantly reduce operating costs, primarily through energy savings. With energy intensity reductions achieved across production processes—such as a decrease from 1340.58 kWh/ton to 1303.78 kWh/ton. The company anticipates a 5-10% reduction in annual energy costs. Additionally, decreased reliance on fossil fuels and improved energy efficiency will lower utility expenses, potentially saving the company upwards of $200,000 annually.
Implementation
Typical business profile
Companies in the glass manufacturing industry can directly benefit from energy efficiency measures and sustainable practices, given the high energy consumption associated with glass production.
Broader manufacturing sectors, including ceramics and metals, can adopt similar energy optimization and waste reduction strategies to lower emissions and improve sustainability.
Approach
Objective
Beta Glass PLC aims to achieve an 8% reduction in energy intensity by implementing advanced technologies and enhancing operational practices within its glass manufacturing processes.
Design Phase: In the design phase, the company evaluates technology solutions to enhance energy efficiency. Options include regenerative burners, which capture and reuse heat, and electric boost technology that uses electric currents to aid the melting process.
Implementation Phase: During implementation, the company scheduled the installation of the new technologies during cold repairs and furnace rebuild periods to minimize disruptions. Staff training on these new technologies is prioritized to ensure effective operation. Additionally, operational adjustments are made to integrate the technologies, such as modifying batch compositions and using real-time monitoring systems for tracking energy usage and emissions. The installation works in three steps: (1) The regenerative technology is installed in the regenerator chambers, which are positioned adjacent to the furnace. These chambers contain heat exchange materials, which absorb the waste heat from the furnace's exhaust. (2) The stored heat is then transferred back into the furnace, where it preheats the combustion air before it enters the furnace. This process increases efficiency by recycling residual heat, reducing the amount of fuel needed for the melting process. (3) Electrical cathode system installed at the bottom as well as the sides of the Furnace: Enhances the furnace operation and reduces fuel usage.
Monitoring and Evaluation Phase: After implementation, the company established key performance indicators (KPIs) to evaluate success. These KPIs include energy intensity reduction, CO2 emissions reduction, and cost savings. Continuous monitoring through energy management systems collects data to track improvements, and regular performance reviews allow for ongoing analysis against set targets.
Furnace Optimization: Electrode and Regenerator Installation at Beta Glass, Agbara Plant. Regeneration fans and electrodes installation were a part of the furnace glass rebuild project. Glass melting furnaces naturally require periodic rebuilds and cold repairs, and these moments are regarded as opportunities to make upgrades that enhance performance. It’s all about consistently optimizing the processes to stay efficient and ahead in the industry.
Stakeholders involved
Required teams and experts:
Mechanical engineers (In-house + Original Equipment Manufacturer (OEM)): - Responsible for the installation of regenerators, aligning, and securing them within the furnace structure. - Ensure mechanical components are fitted correctly to avoid system stress
Electrical engineers (In-house + OEM): - Handle the installation and commissioning of the electrodes - Ensure proper wiring, connections, and integration with the furnace control systems
Refractory specialists (In-house): - Experts in furnace linings to assess and repair or adjust refractory materials during the installation - Handle potential refractory relining around electrodes and regenerators
Instrumentation and control engineers (In-house + OEM): - Set up sensors and control systems that monitor the performance of the electrodes and regenerators. Calibrate and integrate monitoring equipment with the furnace system
Project managers or supervisors (In-house): - Oversee the installation process, ensure timelines are adhered to, and coordinate between teams
HSE (Health, Safety, and Environment) Specialists (In-house): - Ensure all safety protocols are followed during installation to prevent hazards
Rigging and installation technicians (In-house + OEM): - Manage the heavy lifting and placement of electrodes and regenerators. - Operate specialized equipment like cranes or hoists. - Evaluate materials for durability and compatibility
Key parameters to consider
Depending on the size and diameter of the furnace. Ideally it takes approximately 55 days to rebuild a 60 m2 Furnace. It is estimated to extend the furnace's life between 8-10 years depending on the Glass Pull. There are several parameters to indicate performance efficiency (from Melt efficiency culminating into operating cost reduction) and below are some key primary parameters to observe:
Furnace thermal efficiency
Measure the percentage of residual heat retained in the system (target: 85 - 90% for modern regenerators)
Track the reduction in fuel usage after installation. Aim for at least a 10–15% decrease
Energy performance
Monitor energy consumption (e.g., kWh per ton of glass melted) for significant reductions
Temperature Profiles
Ensure consistent high temperatures in the melting and refining zones
Measure the temperature of air preheated by regenerators (typically 1,200–1,300°C for high-efficiency systems)