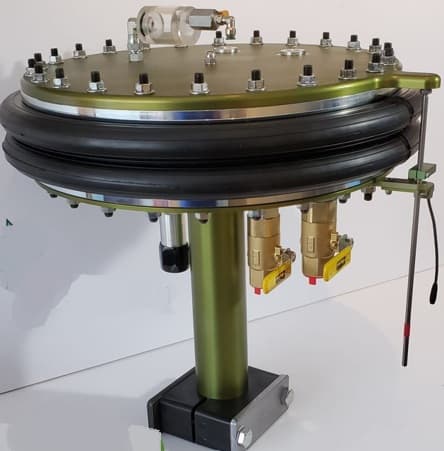
Switch to variable volume oil reservoir in heavy machinery
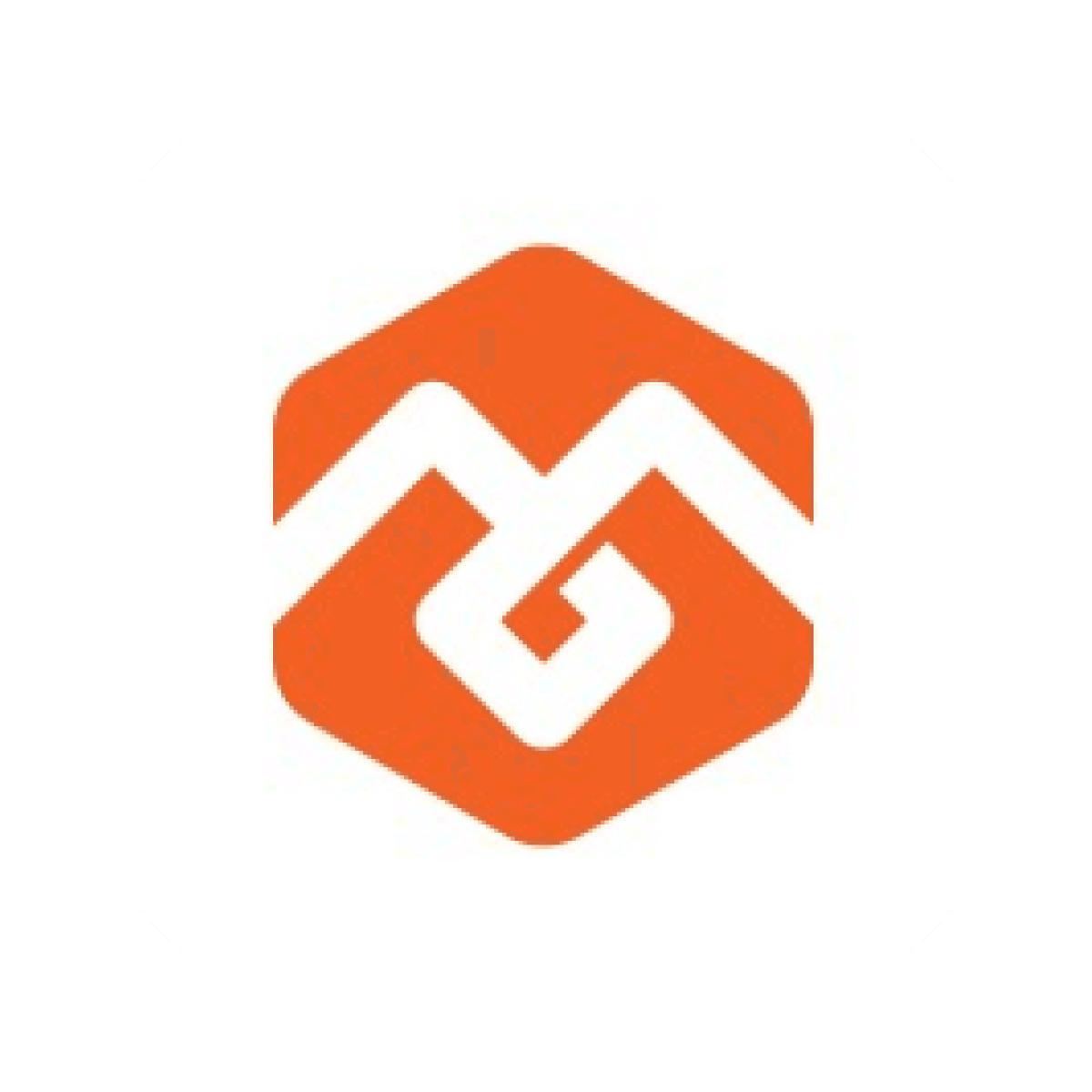
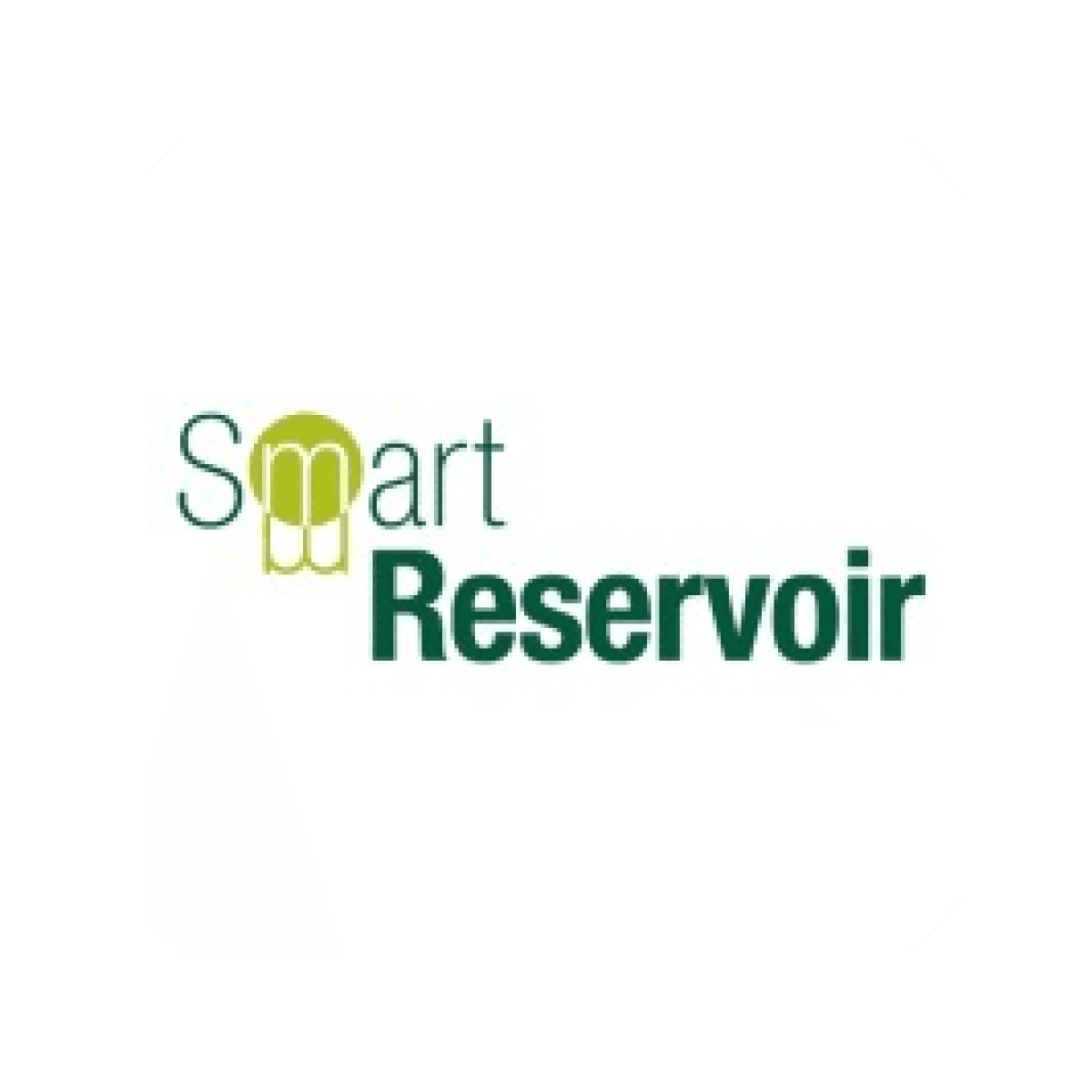
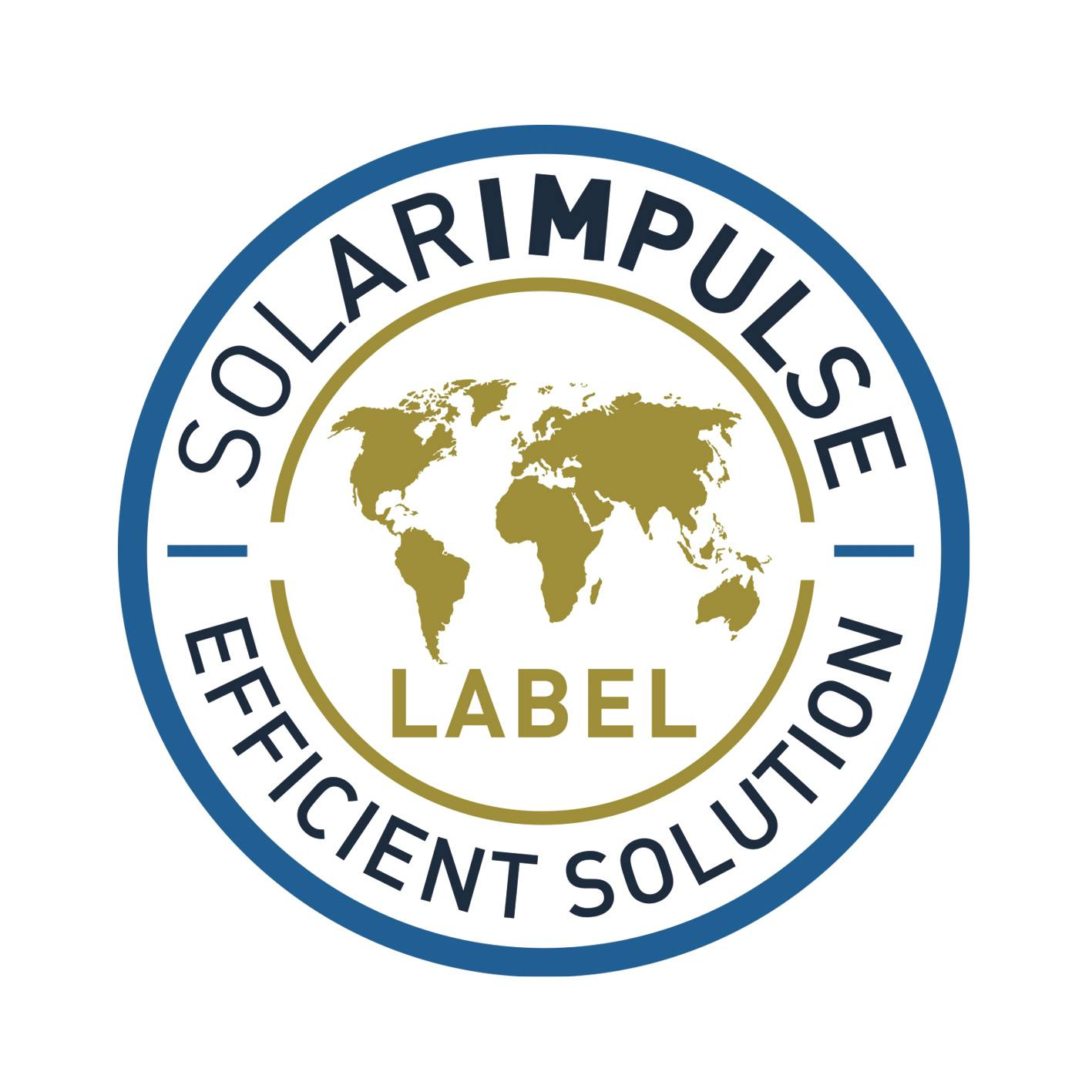
Summary
Traditional hydraulic oil reservoirs in heavy machinery were replaced with Smart Reservoir technology of variable volume reservoirs, resulting in lighter machines and a reduced carbon footprint.
Context
This case-study has been developed in partnership with the Solar Impulse Foundation, which is promoting – through assessing, certifying and facilitating access to finance - the multitude of clean and profitable solutions currently available worldwide. Discover more of Solar Impulse Foundation’s labelled solutions here.
MBI Global, a Canadian manufacturer of prospection drills, recognized the limitations of traditional hydraulic reservoirs used in their machines. These reservoirs were bulky, heavy, and required a large volume of hydraulic fluid, contributing to increased machine weight, transportation costs, and environmental impact. MBI Global sought a solution that would address these challenges while maintaining the performance and reliability of their drilling equipment. Implementing Smart Reservoir technology resulted in a drastic oil volume and weight reduction which has a direct impact on decarbonization.
Solution
MBI Global partnered with Smart Reservoir to implement their innovative reservoir technology called variable volume reservoir (VVR) in their drilling machines. Smart Reservoir's technology utilizes reservoir technology similar to the one used in commercial aircrafts. The core is flexible and reacts to thermal expansion and volume differential. They are sealed from the atmosphere and airless thus protecting the oil from the surrounding contaminants and moisture. The innovative volume sizing technique (1) compared to the classic approach allows to achieve a significant reduction in required size resulting in major weight reduction compared to traditional hydraulic reservoirs. This technology enables the use of significantly less hydraulic fluid without any impact on the drill operation and hydraulic system performance.
MBI Global replaced some of their bulky ~200 liter reservoirs, weighing ~350kg, with Smart Reservoir units ranging from 7 to 21 liters and weighing only 12kg to 60kg. This replacement was implemented across various drill models, including the KmA.3 heli-portable drill and the GT6 & GT8 drills.
The difference between the 2 solutions is drastically different. When a classic reservoir is used, the returning flow enters the reservoir and according to certain rules, the dwell time before the oil is pumped back into the system must be between 3-5 minutes. Consequently, the pump(s) capacity is multiplied by 3 to 5 which gives the reservoir size to use. This results in a reservoir that can be very large and heavy. When a VVR system is used, the returning flow goes directly to the pump inlet with no dwell time. The VVR system is not impacted by the return flow but works like an expansion chamber. This expansion is twofold:
It will react to fluid thermal expansion compensation
It will react to differential cylinder rod volume compensation (only when cylinders are present into the system)
(1) The sizing technique consist of calculating the network oil fill volume in order to estimate the thermal expansion and to calculate the total cylinder rod volume which gives the differential oil volume that the VVR will compensate for.
Impact
Sustainability impact
Climate Impact
The significant reduction in hydraulic fluid usage directly translates to a reduced carbon footprint for MBI Global's drilling operations. The smaller and lighter machines also consume less fuel during transportation, further contributing to emissions reduction.
The GT6 drill model is available with a standard atmospheric reservoir of ~200 liters or a sealed-airless smart reservoir of 21 liters providing the same performance. The estimated GHG emitted to produce 200 liters of oil is 275 kg CO2e compared with 29 kg CO2e for the smart reservoir 21 liters. Furthermore, over a 10-year period the standard reservoir which is vented to the atmosphere will require 4 oil changes (& disposals) mainly because of oil contamination by solid particles and moisture ingestion. This represents a GHG of 1100 kg CO2e. Since the smart reservoir is sealed and airless, making the system protected from the harsh surrounding environment, it requires only 2 oil changes over 10 years, resulting in a GHG of 58 kg CO2e. The GHG to dispose the oil is not accounted for. The weight comparison is quite important when full, the standard reservoir is ≈350 kg compared to 73 kg for a smart reservoir 21 liters units, which reflects into a significative impact on transportation cost.
Ref.: Values are based on the following assumptions: Emission factor of 1.4 tons CO2 per ton of mineral based hydraulic fluid (1,375 kg CO2e / L).
Nature impact
By using less hydraulic fluid, the technology minimizes the potential for spills and leaks, protecting the environment from contamination.
Business impact
Benefits
The implementation of smart reservoir technology has resulted in several benefits for MBI Global:
Up to 90% in volume reduction of used oil in drill machinery over 10 years
The reduced machine weight makes the drills easier to transport, lowering transportation costs and expanding their reach to remote locations
The smaller reservoirs also make it more affordable for operators to use biodegradable fluids, which are often more expensive but environmentally preferable and sometimes compulsory
Costs
The initial cost of acquiring and installing the smart reservoir technology represents the primary expense. The initial purchasing cost of the standard reservoir with mineral oil is ~30% less expensive. However, the long-term savings in transportation costs, reduced fluid consumption, and potential for increased sales due to the appeal of biodegradable fluids can offset this initial investment. Eg. with biodegradable oil it becomes ~27% more expensive. Furthermore, after 10-12 years of operation (after 4 oil changes compared with 2 oil changes with the smart reservoir) the cost ratio becomes 44:1.
Implementation
Typical business profile
The smart reservoir technology is most relevant for businesses in industries that rely on hydraulic systems in their operations, particularly those operating in remote or challenging environments where weight and transportation costs are significant factors. This includes:
Mining
Construction
Marine
Agriculture
Oil and gas exploration
Other sectors where heavy machinery is used
Approach
MBI Global's approach to implementing smart reservoir technology involved a collaborative effort with the solution provider’s team:
The process began with identifying suitable drilling rig models for retrofitting with the new reservoirs.
The KmA.3 heli-portable drill and the GT6 & GT8 drills were selected due to their large, heavy traditional reservoirs and their frequent deployment to remote locations.
The implementation process first started with the KmA.3 model in 2007 to demonstrate the benefits. It involved replacing the existing traditional hydraulic reservoirs of 220 liters with smart reservoir's VVR400 model of 7 liters. This required modifications to the drilling rigs' hydraulic systems to accommodate the smaller reservoirs and ensure proper functionality. MBI Global worked closely with smart reservoir's engineers to ensure a seamless integration and to optimize the performance of the new reservoirs.
Later on, a larger model (VVR1300 of 21 liters) was implemented to the larger GT6 & GT8 drill models mounted on wheels and tracks vehicles replacing their traditional reservoir of ~200 liters.
Stakeholders involved
Project leads: Engineering and product development teams from MBI Global, along with technical experts from Smart Reservoir
Company functions: MBI Global's procurement, manufacturing, and field service teams were also involved in the implementation process
Main providers: Smart Reservoir
Key parameters to consider:
Reservoir size and capacity: the technology offers various VVR models with different capacities. It's crucial to select the appropriate size based on the specific hydraulic system requirements of the machinery
Fluid compatibility: Ensure that the hydraulic fluid used is compatible with the smart reservoir technology and the materials used in its construction
Operating conditions: Consider the environmental conditions in which the machinery will operate, like temperature range and machine differential volume requirements which will dictate the reservoir size needed. They can be adapted for salty environment like for marine & subsea system
Regulatory compliance: Ensure the technology complies with relevant safety and environmental regulations.
Implementation and operations tips
Main challenge faced during implementation: the main challenge for the VVR implementation is to make the design team, technicians and operators understand this new technology.
How to overcome this challenge: To focus on training is the best way to get the VVR implementation and operation accepted by technicians, machine owners and operators.
Other tips for implementation, operation, and long-term success and management:
Thorough planning: Conduct a detailed assessment of the existing hydraulic system and its requirements before selecting and installing a Smart Reservoir
Professional installation: Engage qualified technicians or engineers to install and integrate the Smart Reservoir technology to ensure proper functionality and safety
Designers training: To properly implement the reservoir into a new concept, Smart Reservoir must give guide lines and support to the engineers mainly for the required size calculations
Operator training: Provide training to machine operators on the proper operation and maintenance of the Smart Reservoir system
Sales & awareness: On the sales point of view, it is quite challenging to convince new prospects to accept the idea that such a small volume reservoir technology can replace a much larger classic reservoir
Monitoring and feedback: Monitor the performance of the Smart Reservoir system and collect feedback from operators to identify any potential issues or areas for improvement