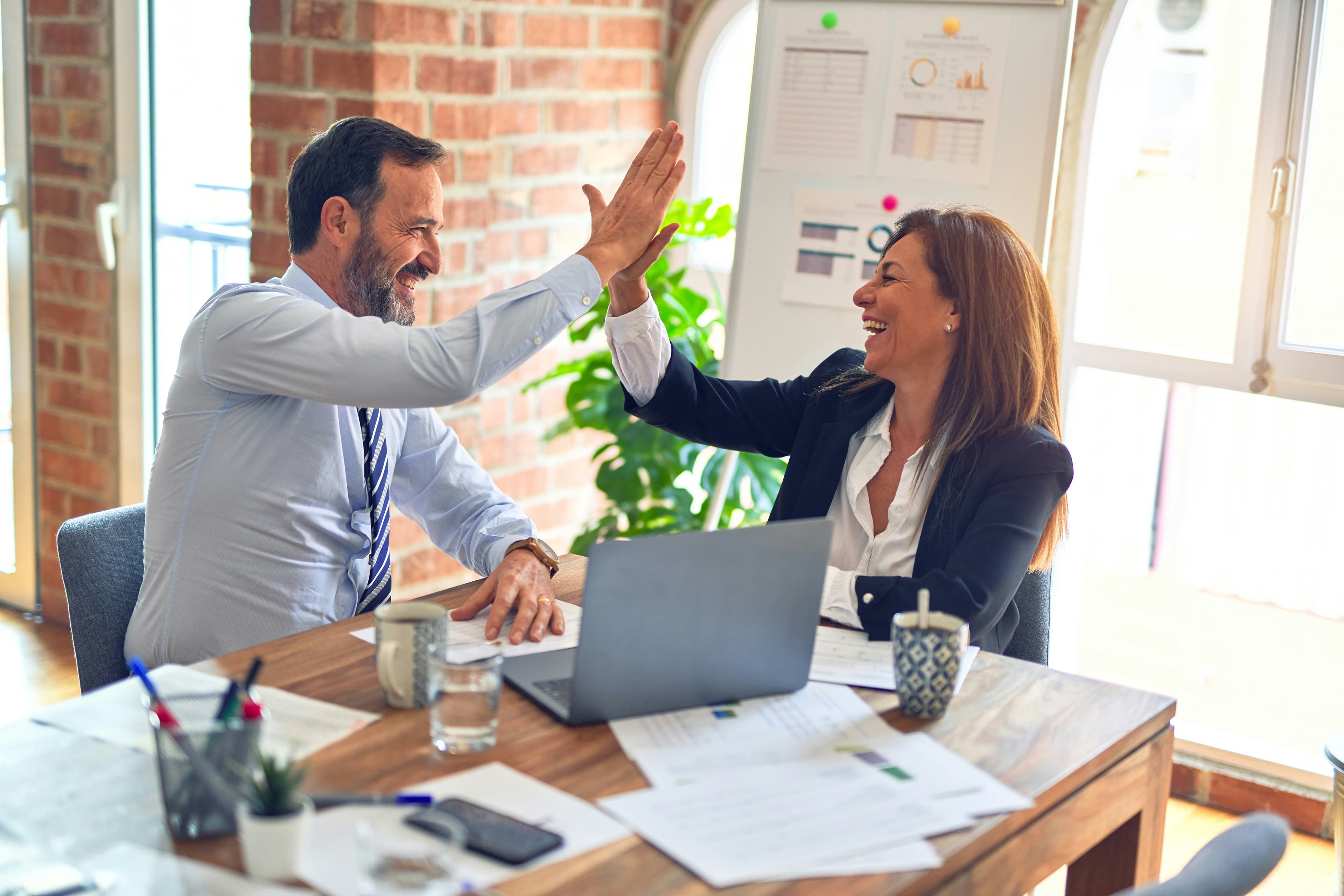
Map suppliers’ ESG progress on Scope 3 with maturity levels
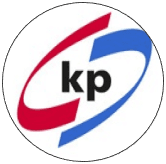
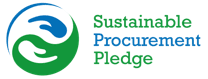
Summary
Klöckner Pentaplast engaged their top 50 suppliers, classifying them into four different maturity levels, to reduce Scope 3 emissions.
Context
This case study is part of The Guide, an initiative that aims to inspire & empower procurement professionals committed to driving sustainability, launched by the Sustainable Procurement Pledge Champion Program. It includes ugly truths, best practices, and case studies across a range of industries and sustainability topics. Learn more here.
Klöckner Pentaplast (KP) is a multinational manufacturer of plastic packaging products.
The case study helps to tackle collaboration with suppliers on Scope 3 emissions. The team has identified the company’s top 50 suppliers, based on Scope 3 emission contribution from category 3.1 - purchased goods and services - and approached them with several questions about GHG emissions, with support from a consultancy. With this supplier engagement program, the company aims to promote sustainable practices in its supply chain and reduce its Scope 3 emissions. Based on 2021 data, these 50 suppliers cover 57% of the company’s total Scope 3 emissions and are responsible for 58% of its total spend.
Solution
The procurement department identified the top 50 suppliers contributing to Scope 3 emissions and engaged them with a questionnaire about GHG emissions, supported by a consultancy. This initiative aimed to promote sustainable practices and reduce Scope 3 emissions.
Suppliers were classified into four maturity levels: advanced, high, medium, and low. The project measured outcomes using KPIs such as response rate, GHG emissions evaluation, and the number of advanced and high-level suppliers identified.
Impact
Sustainability Impact
Climate Impact
GHG Scope | Impact |
Scope 1 | Not applicable |
Scope 2 | Not applicable |
Scope 3 | 57% of total Scope 3 emissions covered by top 50 suppliers (including category 3.1) |
Nature Impact
Promoted sustainable practices in the supply chain also related to impacts on nature.
Social Impact
Raised awareness about sustainability and CO2 reduction.
Business impact
Benefits
The initiative is considered beneficial in the company’s strategy to comply with international sustainability regulations and reporting standards
The program enhances overall supplier relationships and engagement. The project provided a comprehensive overview of supplier maturity in climate change actions, allowing for specific follow-ups to improve performance.
The initiative has laid a new foundation for Scope 3 reduction tracking with LCA values from suppliers.
Costs
The investment came from the central procurement budget and related mainly to staff costs
Outsourcing to a specialized consulting firm is recommended if budget allows
Abatement costs
Not specified
Co-benefits
Improved supplier engagement and collaboration.
Potential side-effects
No potential negative side-effects identified.
Implementation
Typical business profile
Relevant for large companies with significant Scope 3 emissions from purchased goods and services.
Approach
Step-by-step approach:
Carefully select the suppliers which are added to the program – in this initiative they were selected based on their Scope 3 emission contribution. But they can also be selected based on spend or volume or take a mixed approach.
Define questions that you would like to ask your suppliers in relation to sustainability. Divide them into different sections and come up with a points system. Outsource work to an external consulting firm, which is specialized in sustainability, if your budget allows.
Classify the suppliers in different maturity levels based on the points achieved - advanced, high, medium and low.
Define specific follow up actions depending on the maturity level.
The outcome was measured with KPIs including how many suppliers answered the questionnaire, the percentage of suppliers we were able to evaluate GHG emissions for and the number of advanced and high-level suppliers were identified as a result of the project.
Stakeholders involved
Group Procurement Manager Sustainability & ESG: Led the initiative and engaged suppliers
External Consultants: Supported supplier engagement and provided expertise
CPO and Group Procurement Director: Sponsored the initiative
Key parameters to consider
The initiative took approximately three months for preparation and development, and three months for implementation.
Implementation and operations tips
Carefully select suppliers based on emissions, spend, or volume
Outsource to a consultancy if resources are limited
Consider supplier selection criteria and ensure high response rate